What Is A Prime Cost In Accounting
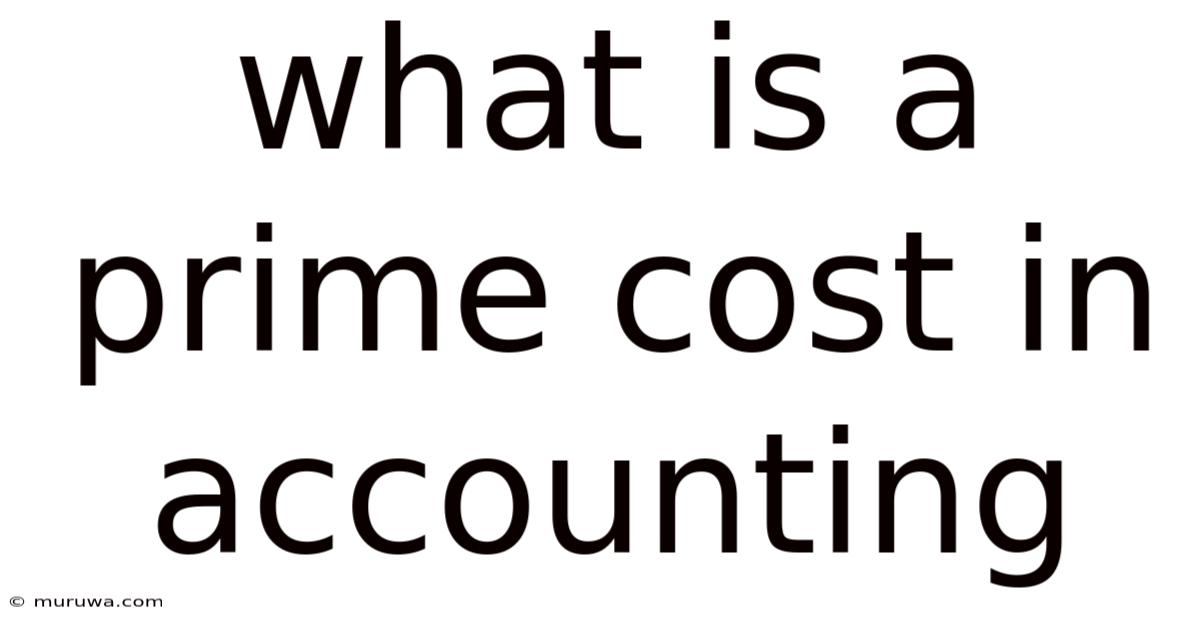
Discover more detailed and exciting information on our website. Click the link below to start your adventure: Visit Best Website meltwatermedia.ca. Don't miss out!
Table of Contents
Decoding Prime Cost: A Comprehensive Guide for Accountants and Business Owners
What if accurate prime cost calculation is the key to unlocking your business's true profitability? Understanding this fundamental accounting concept is crucial for informed decision-making and sustained success.
Editor’s Note: This article on prime cost in accounting was published today, offering readers the latest insights and understanding of this critical financial metric. This comprehensive guide will equip you with the knowledge to effectively calculate and utilize prime cost data for optimal business management.
Why Prime Cost Matters: Relevance, Practical Applications, and Industry Significance
Prime cost, a core element of cost accounting, represents the direct costs involved in manufacturing a product or providing a service. It's a crucial metric for businesses seeking to understand their production expenses, optimize pricing strategies, and improve overall profitability. Accurate prime cost calculation allows for better budgeting, cost control, and informed decision-making related to production processes, resource allocation, and pricing strategies. Across various industries, from manufacturing and construction to hospitality and retail, understanding prime cost is paramount for competitive advantage.
Overview: What This Article Covers
This article provides a comprehensive exploration of prime cost, covering its definition, components (direct materials and direct labor), calculation methods, importance in different industries, limitations, and its relationship with other cost accounting concepts like conversion cost and total cost. Readers will gain a practical understanding of how to calculate prime cost, interpret the results, and utilize this knowledge for effective business management.
The Research and Effort Behind the Insights
This article is the result of extensive research, drawing upon established accounting principles, industry best practices, and real-world examples. The information presented is supported by credible sources and aims to provide readers with accurate and reliable information for informed decision-making. A structured approach has been employed to ensure clarity and easy comprehension of the subject matter.
Key Takeaways:
- Definition and Core Concepts: A clear definition of prime cost and its foundational elements.
- Practical Applications: Real-world examples of prime cost calculation across various industries.
- Challenges and Limitations: Potential pitfalls in prime cost calculation and strategies for mitigation.
- Relationship to Other Costs: Understanding the connection between prime cost, conversion cost, and total cost.
- Decision-Making Applications: How prime cost data informs strategic decisions related to pricing, production, and resource allocation.
Smooth Transition to the Core Discussion
Having established the significance of prime cost, let's delve into a detailed examination of its components, calculation, applications, and limitations.
Exploring the Key Aspects of Prime Cost
1. Definition and Core Concepts:
Prime cost is the sum of direct materials and direct labor costs incurred in the production of goods or services. Direct materials are the raw materials directly used in the manufacturing process, easily traceable to the finished product. Direct labor represents the wages and benefits paid to employees directly involved in the production process. These costs are easily identifiable and directly attributable to the creation of a specific product or service.
2. Applications Across Industries:
-
Manufacturing: In manufacturing, prime cost is crucial for determining the cost of goods sold (COGS), setting selling prices, and evaluating the efficiency of production processes. A car manufacturer, for instance, would include the cost of steel, rubber, and other raw materials as direct materials, and the wages of assembly line workers as direct labor in calculating the prime cost of a vehicle.
-
Construction: Construction projects heavily rely on prime cost calculations. Direct materials encompass cement, bricks, lumber, and other building materials, while direct labor includes the wages of construction workers, electricians, and plumbers.
-
Food Service: Restaurants and other food service establishments use prime cost to determine the cost of goods sold for menu items. Direct materials include ingredients like meat, vegetables, and spices, and direct labor comprises the wages of cooks and kitchen staff.
-
Retail: While less directly applicable than in manufacturing, some retail businesses, particularly those involved in assembling or customizing products, can use prime cost to track the cost of adding value to products before resale.
3. Challenges and Solutions:
Calculating prime cost can present challenges, particularly in complex manufacturing environments or when dealing with indirect costs that may be mistakenly included. Some common challenges include:
-
Accurate Material Costing: Fluctuations in raw material prices can impact accuracy. Effective inventory management and accurate cost tracking systems are crucial for reliable calculations.
-
Labor Cost Allocation: Accurately assigning labor costs to specific products can be complex, especially in environments with shared resources or overlapping tasks. Time-tracking systems and proper labor allocation methodologies are needed.
-
Overhead Costs: Distinguishing between direct and indirect costs is critical. Indirect costs (e.g., factory rent, utilities) are excluded from prime cost and must be carefully separated.
Solutions:
- Implement robust inventory management systems.
- Use accurate time-tracking and labor allocation methods.
- Develop a clear cost accounting system to differentiate between direct and indirect costs.
- Regularly review and update cost data to reflect market fluctuations and operational changes.
4. Impact on Innovation:
Understanding prime cost enables businesses to identify areas for cost optimization and innovation. By analyzing the cost components, companies can explore alternative materials, improve production processes, and negotiate better deals with suppliers, leading to enhanced efficiency and profitability.
Closing Insights: Summarizing the Core Discussion
Prime cost serves as a foundational element in cost accounting, providing vital insights into the direct costs associated with production. By accurately calculating and analyzing prime cost, businesses can optimize their operations, improve pricing strategies, and make informed decisions leading to enhanced profitability and sustainable growth.
Exploring the Connection Between Overhead Costs and Prime Cost
Overhead costs represent indirect expenses necessary for production but not directly traceable to a specific product. They stand in contrast to the direct costs that comprise prime cost. While overhead costs are not included in prime cost calculations, understanding their relationship is essential for a complete cost analysis. Ignoring overhead costs can lead to inaccurate cost estimations and potentially flawed pricing strategies.
Key Factors to Consider:
Roles and Real-World Examples: Overhead costs include rent, utilities, depreciation of equipment, and supervisory salaries. For a manufacturing company, factory rent is an overhead cost, while the wages of assembly line workers are direct labor costs.
Risks and Mitigations: Underestimating overhead costs can lead to underpricing products and reduced profitability. Accurate allocation of overhead costs through methods like activity-based costing (ABC) can mitigate this risk.
Impact and Implications: The inclusion or exclusion of overhead costs significantly impacts the overall cost of production and profitability. Accurate cost accounting considering both direct and indirect costs is crucial for making informed business decisions.
Conclusion: Reinforcing the Connection
The relationship between overhead costs and prime cost highlights the importance of a comprehensive cost accounting system. While prime cost focuses on direct costs, understanding and accurately allocating overhead costs provides a complete picture of the total cost of production, enabling more accurate pricing, better resource allocation, and improved profitability.
Further Analysis: Examining Overhead Costs in Greater Detail
Overhead costs can be further categorized into fixed and variable overhead costs. Fixed overhead costs remain relatively constant regardless of production volume (e.g., rent, depreciation), while variable overhead costs fluctuate with production volume (e.g., utilities, indirect materials). Understanding this distinction helps in more accurate cost forecasting and budgeting. Various methods exist for allocating overhead costs, including the traditional method and more sophisticated methods like activity-based costing (ABC), which aims to allocate overhead costs more accurately based on the activities that drive those costs.
FAQ Section: Answering Common Questions About Prime Cost
What is prime cost?
Prime cost is the sum of direct materials and direct labor costs incurred in the production of goods or services.
How is prime cost calculated?
Prime cost is calculated by adding the total direct materials cost to the total direct labor cost.
What is the difference between prime cost and total cost?
Prime cost only includes direct materials and direct labor costs. Total cost includes prime cost plus all overhead costs.
Why is prime cost important?
Prime cost is crucial for pricing decisions, cost control, performance evaluation, and profitability analysis.
How can I improve the accuracy of my prime cost calculations?
Implementing robust inventory management, accurate time-tracking systems, and a clear cost accounting system are vital for accurate prime cost calculation.
Practical Tips: Maximizing the Benefits of Prime Cost Analysis
- Understand the Basics: Thoroughly grasp the definition and components of prime cost.
- Accurate Data Collection: Implement reliable systems for tracking direct materials and labor costs.
- Regular Monitoring: Regularly review and analyze prime cost data to identify trends and areas for improvement.
- Cost Control Measures: Implement strategies to control direct materials and labor costs, such as negotiating better supplier prices or improving production efficiency.
- Integration with Other Costing Methods: Combine prime cost analysis with other costing techniques (e.g., activity-based costing) for a more holistic understanding of costs.
Final Conclusion: Wrapping Up with Lasting Insights
Prime cost, a cornerstone of cost accounting, provides invaluable insights into the direct costs of production. By mastering the calculation and interpretation of prime cost, businesses can enhance their pricing strategies, optimize resource allocation, improve efficiency, and ultimately, boost their profitability. Understanding the relationship between prime cost, overhead costs, and total costs offers a holistic view of the complete cost structure, empowering businesses to make informed decisions for sustainable growth and competitive advantage. Accurate and timely prime cost analysis is essential for ensuring a business's long-term financial health and success.
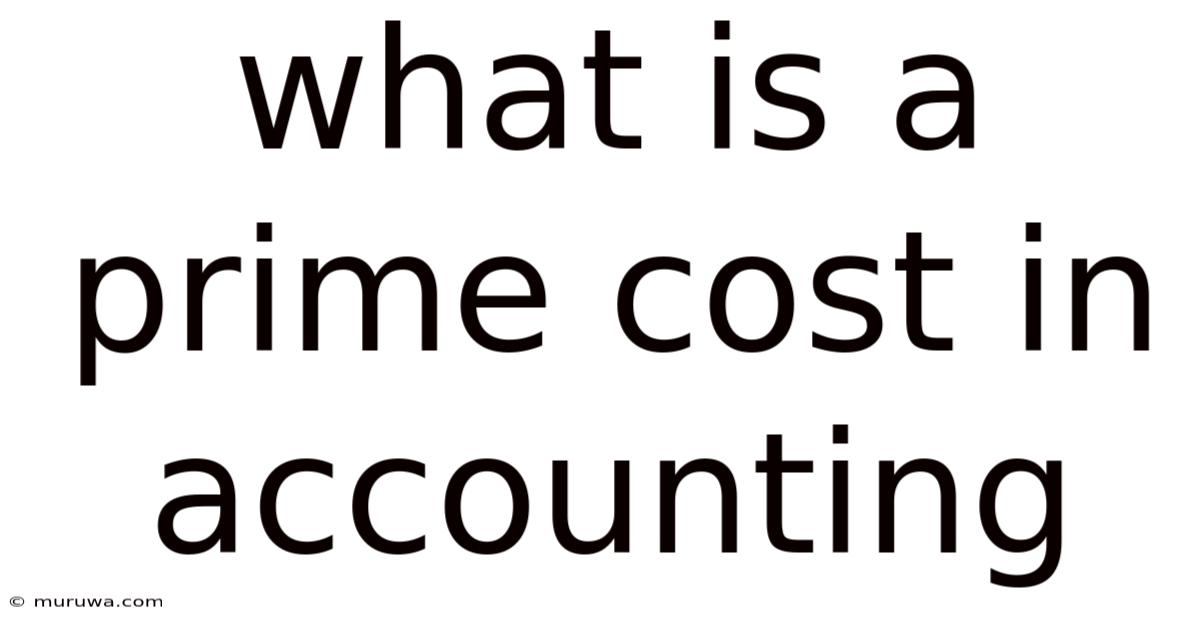
Thank you for visiting our website wich cover about What Is A Prime Cost In Accounting. We hope the information provided has been useful to you. Feel free to contact us if you have any questions or need further assistance. See you next time and dont miss to bookmark.
Also read the following articles
Article Title | Date |
---|---|
Ballot Definition | Apr 13, 2025 |
What Is A Small Businesss Best Return On Investment | Apr 13, 2025 |
What Does A Credit Balance On A Bill Mean | Apr 13, 2025 |
How To Close A Small Business | Apr 13, 2025 |
What Kind Of Credit Score Do You Need For A Parent Plus Loan | Apr 13, 2025 |