What Are Holding Costs Definition How They Work And Example
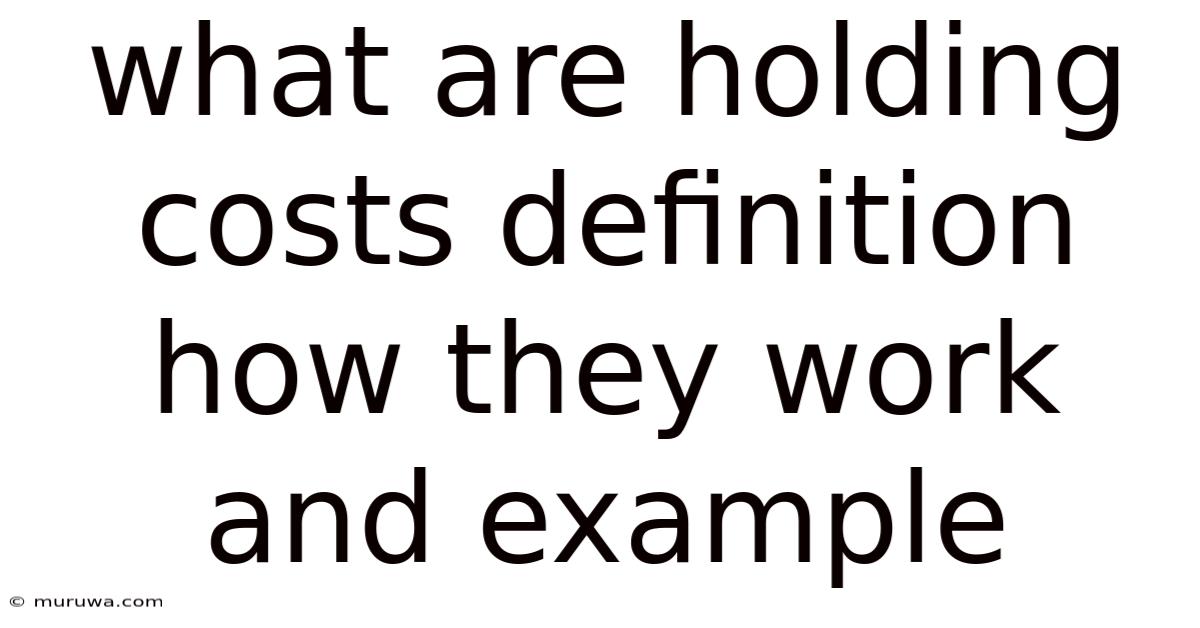
Discover more detailed and exciting information on our website. Click the link below to start your adventure: Visit Best Website meltwatermedia.ca. Don't miss out!
Table of Contents
Unlocking the Secrets of Holding Costs: Definition, Mechanics, and Real-World Examples
What if the success of your business hinges on effectively managing a seemingly insignificant aspect of operations? Understanding and optimizing holding costs is not just about saving money; it's about unlocking significant competitive advantages and driving profitability.
Editor's Note: This article provides a comprehensive guide to holding costs, exploring their definition, calculation, impact, and effective management strategies. Updated with the latest insights and real-world examples, this guide will empower businesses of all sizes to optimize their inventory management and boost their bottom line.
Why Holding Costs Matter: Relevance, Practical Applications, and Industry Significance
Holding costs, also known as carrying costs or inventory holding costs, represent the total cost of storing and maintaining inventory. While often overlooked, these costs significantly impact profitability. They’re a critical component of total inventory management expenses and directly influence pricing strategies, production planning, and overall business efficiency. Industries from manufacturing and retail to healthcare and technology experience these costs, making understanding and controlling them crucial for competitive success. Ignoring holding costs can lead to diminished profit margins, increased waste, and lost opportunities.
Overview: What This Article Covers
This article delves into the intricacies of holding costs. We will define the concept, explore the various components that contribute to these costs, examine how they are calculated, and provide practical examples across different industries. Furthermore, we'll explore strategies for reducing holding costs and highlight the importance of optimizing inventory management for improved profitability and efficiency.
The Research and Effort Behind the Insights
This article draws upon extensive research, incorporating data from industry reports, case studies from successful businesses, and best practices from supply chain management experts. The analysis presented aims to provide readers with accurate, actionable insights backed by reliable sources and evidence-based recommendations.
Key Takeaways:
- Definition and Core Concepts: A thorough understanding of holding costs and their components.
- Calculation Methods: Practical formulas and techniques for calculating holding costs.
- Practical Applications: Real-world examples demonstrating the impact of holding costs across various industries.
- Reduction Strategies: Effective techniques for minimizing holding costs and improving profitability.
- Impact on Business Decisions: How understanding holding costs can improve inventory management and strategic planning.
Smooth Transition to the Core Discussion
With a foundational understanding of the importance of holding costs, let's now delve into a deeper exploration of their key aspects.
Exploring the Key Aspects of Holding Costs
1. Definition and Core Concepts:
Holding costs encompass all expenses associated with storing and maintaining unsold inventory. These costs are incurred from the moment goods are received into storage until they are sold or used. Unlike direct costs (materials, labor, manufacturing), holding costs are indirect, often hidden within broader operational expenses. However, their impact on profitability is undeniable.
2. Components of Holding Costs:
Several key components constitute holding costs. These include:
- Storage Costs: Rent or lease payments for warehouse space, utilities (electricity, heating, cooling), security systems, and insurance for the facility and inventory.
- Insurance Costs: Premiums paid to protect inventory against damage, theft, or loss.
- Taxes: Property taxes on the warehouse and potentially inventory taxes depending on location and regulations.
- Obsolescence Costs: The loss of value due to product becoming outdated or unmarketable. This is particularly relevant for technology or fashion industries.
- Depreciation Costs: Loss of value due to wear and tear, damage, or spoilage, particularly for perishable goods.
- Inventory Shrinkage: Losses due to theft, damage, spoilage, or errors in counting.
- Capital Costs: The opportunity cost of the capital tied up in inventory. This is the return that could have been earned by investing that capital elsewhere. This is often calculated as a percentage of the inventory's value.
- Handling Costs: Expenses related to moving, handling, and managing inventory within the warehouse. This includes labor costs for workers, equipment maintenance, and potential damage during handling.
3. Calculating Holding Costs:
Calculating holding costs requires careful consideration of each component. A common approach involves expressing holding costs as a percentage of the average inventory value. The formula often used is:
Holding Cost Percentage = (Storage Costs + Insurance Costs + Taxes + Obsolescence Costs + Depreciation Costs + Inventory Shrinkage + Capital Costs + Handling Costs) / Average Inventory Value
The average inventory value is calculated as (Beginning Inventory + Ending Inventory) / 2.
4. Applications Across Industries:
The impact of holding costs varies across industries. For example:
- Retail: High-volume retailers with perishable goods (groceries) face significant obsolescence and spoilage costs. Fashion retailers face high obsolescence costs due to rapidly changing trends.
- Manufacturing: Manufacturers hold raw materials, work-in-progress, and finished goods, leading to substantial storage and capital costs.
- Technology: Rapid technological advancements create substantial obsolescence costs in the technology sector. Holding outdated components or products can lead to significant financial losses.
- Pharmaceuticals: Strict regulatory requirements and temperature-sensitive products lead to high storage and handling costs.
5. Impact on Innovation:
High holding costs can discourage innovation by increasing the risk associated with developing and launching new products. Businesses might be hesitant to invest in new product lines if they anticipate significant carrying costs for unsold inventory. Efficient inventory management, therefore, is directly linked to a company's ability to adapt to market changes and introduce new products successfully.
Closing Insights: Summarizing the Core Discussion
Holding costs are a critical aspect of inventory management. Ignoring them can lead to significant financial losses and hinder business growth. By understanding the components, calculating the total cost, and implementing effective strategies for reduction, businesses can significantly improve profitability and competitiveness.
Exploring the Connection Between Inventory Turnover and Holding Costs
Inventory turnover rate is directly related to holding costs. A high inventory turnover rate (meaning inventory is sold quickly) signifies lower holding costs because inventory spends less time in storage. Conversely, a low turnover rate implies higher holding costs due to prolonged storage periods.
Key Factors to Consider:
- Roles and Real-World Examples: Companies with efficient supply chain management and just-in-time inventory systems typically have lower inventory turnover rates and, consequently, lower holding costs. Conversely, companies with inefficient processes and excessive stock often experience higher holding costs.
- Risks and Mitigations: Overstocking is a major risk, increasing holding costs and potentially leading to obsolescence. Implementing demand forecasting and inventory control systems helps mitigate this risk.
- Impact and Implications: Lower holding costs improve profitability and free up capital for other investments, driving business growth. High holding costs can strain cash flow, limit expansion opportunities, and reduce competitiveness.
Conclusion: Reinforcing the Connection
The relationship between inventory turnover and holding costs underscores the importance of efficient inventory management. Strategies that improve turnover directly reduce holding costs, leading to a more profitable and agile business.
Further Analysis: Examining Inventory Control Systems in Greater Detail
Effective inventory control systems are crucial for managing holding costs. These systems employ techniques such as:
- Just-in-Time (JIT) Inventory: Minimizing inventory levels by receiving materials only when needed for production.
- Economic Order Quantity (EOQ): Determining the optimal order size to minimize the total cost of ordering and holding inventory.
- First-In, First-Out (FIFO) and Last-In, First-Out (LIFO): Methods for managing inventory flow to minimize obsolescence and spoilage.
- Demand Forecasting: Accurately predicting future demand to optimize inventory levels and reduce overstocking.
- Inventory Management Software: Utilizing software to track inventory levels, manage orders, and analyze trends.
FAQ Section: Answering Common Questions About Holding Costs
Q: What is the most significant component of holding costs for my business?
A: The most significant component will vary depending on your industry and business model. For retailers with perishable goods, it's often obsolescence and spoilage. For manufacturers, it might be capital costs or storage costs. Careful analysis of your own expenses is crucial to identify the largest contributors.
Q: How can I reduce my holding costs without compromising customer service?
A: Implementing efficient inventory control systems, accurate demand forecasting, and potentially adopting a just-in-time inventory approach can help reduce costs without impacting customer service.
Practical Tips: Maximizing the Benefits of Holding Cost Optimization
- Conduct a thorough analysis of your current holding costs: Identify the key contributors and areas for improvement.
- Implement an inventory management system: Choose a system that suits your business needs and provides real-time data on inventory levels.
- Improve demand forecasting: Utilize accurate forecasting techniques to optimize ordering and reduce overstocking.
- Negotiate better storage rates: Explore options for reducing warehousing costs through negotiation or exploring alternative storage solutions.
- Implement effective inventory control methods: Utilize FIFO or LIFO methods to minimize obsolescence.
Final Conclusion: Wrapping Up with Lasting Insights
Holding costs represent a significant yet often overlooked aspect of business operations. Understanding and effectively managing these costs is crucial for maximizing profitability and achieving sustainable growth. By implementing the strategies and techniques discussed in this article, businesses can significantly improve efficiency, reduce expenses, and gain a competitive edge in the marketplace. The journey towards effective holding cost management requires continuous monitoring, analysis, and adaptation to changing market conditions. But the rewards – increased profitability, improved cash flow, and enhanced business agility – make it a worthwhile endeavor for any organization.
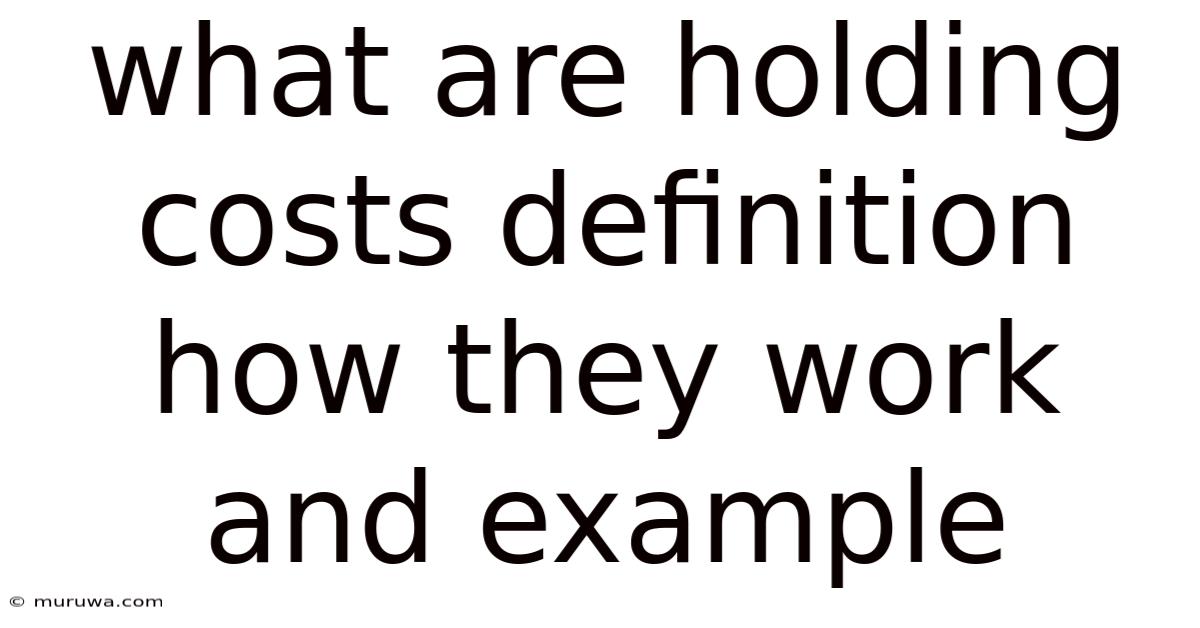
Thank you for visiting our website wich cover about What Are Holding Costs Definition How They Work And Example. We hope the information provided has been useful to you. Feel free to contact us if you have any questions or need further assistance. See you next time and dont miss to bookmark.
Also read the following articles
Article Title | Date |
---|---|
Give Up Definition Parties And Example Of A Give Up Trade | Apr 26, 2025 |
General Partnerships Definition Features And Example | Apr 26, 2025 |
Gazunder Definition | Apr 26, 2025 |
Government Securities Clearing Corporation Gscc Definition | Apr 26, 2025 |
Goldilocks Economy Definition What Makes It Work | Apr 26, 2025 |