Minimum Guaranteed Fill Mgf Order Definition
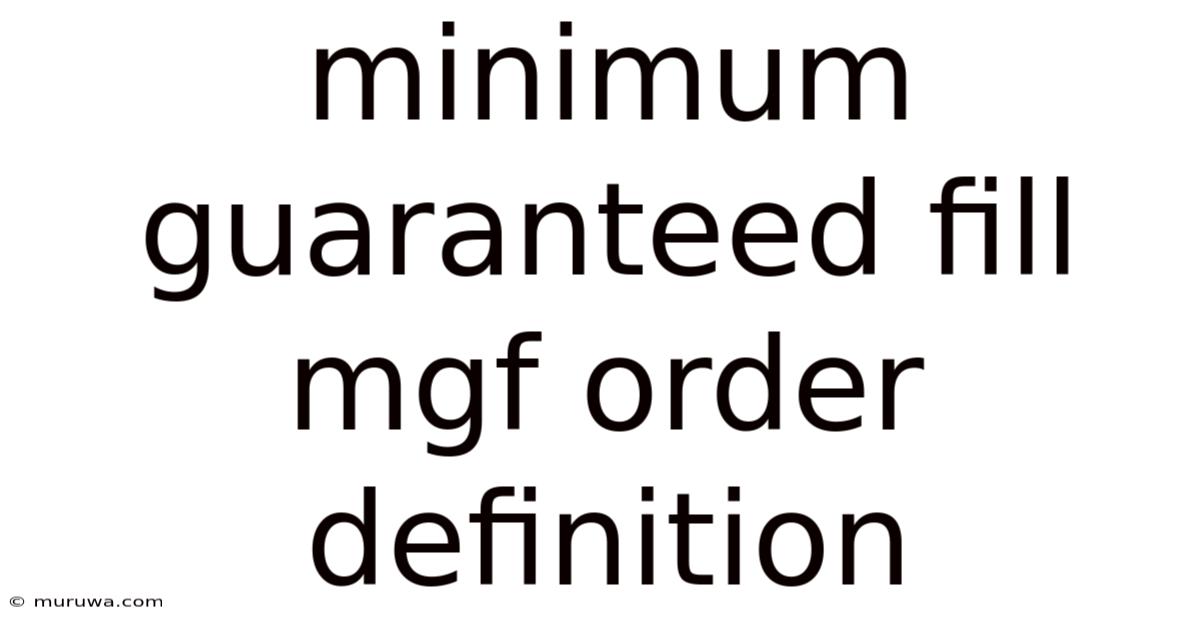
Discover more detailed and exciting information on our website. Click the link below to start your adventure: Visit Best Website meltwatermedia.ca. Don't miss out!
Table of Contents
Decoding Minimum Guaranteed Fill (MGF) Orders: A Comprehensive Guide
What if the future of efficient order fulfillment hinges on understanding Minimum Guaranteed Fill (MGF) orders? This critical concept is transforming supply chain management and optimizing order processing for businesses of all sizes.
Editor’s Note: This article on Minimum Guaranteed Fill (MGF) orders provides a detailed exploration of this crucial aspect of order management. It’s designed to give supply chain professionals, business owners, and anyone interested in optimizing order fulfillment a comprehensive understanding of MGFs and their implications.
Why Minimum Guaranteed Fill Matters:
In today's fast-paced e-commerce environment, efficient order fulfillment is paramount. Customers expect speedy delivery and complete orders. Minimum Guaranteed Fill (MGF) orders are a crucial element in ensuring this expectation is met. Understanding MGFs allows businesses to manage inventory effectively, optimize shipping processes, and ultimately improve customer satisfaction. This, in turn, can lead to increased sales, reduced operational costs, and a stronger competitive edge. MGFs are relevant across various sectors, from retail and manufacturing to pharmaceuticals and technology, impacting inventory planning, logistics, and overall business strategy.
Overview: What This Article Covers:
This article provides a deep dive into the world of Minimum Guaranteed Fill orders. We'll define MGFs, explore their practical applications, analyze the challenges involved in implementing them, and examine their future implications. We'll also explore the connection between MGFs and other crucial aspects of supply chain management, such as inventory management and order processing. Readers will gain actionable insights and a clear understanding of how to leverage MGFs to optimize their own operations.
The Research and Effort Behind the Insights:
This comprehensive guide is the culmination of extensive research, drawing upon industry best practices, case studies from diverse sectors, and analysis of leading supply chain management methodologies. The information presented is supported by credible data sources and aims to provide accurate, reliable, and actionable insights for readers.
Key Takeaways:
- Definition and Core Concepts: A precise explanation of MGF orders and their underlying principles.
- Practical Applications: Real-world examples of how MGFs are implemented across various industries.
- Challenges and Solutions: Key obstacles in implementing MGFs and strategies to overcome them.
- Future Implications: The long-term impact of MGFs on supply chain management and e-commerce.
Smooth Transition to the Core Discussion:
Now that we understand the significance of Minimum Guaranteed Fill (MGF) orders, let's delve into their core aspects. We will begin by defining MGF orders and then explore their practical applications, associated challenges, and potential future implications.
Exploring the Key Aspects of Minimum Guaranteed Fill (MGF) Orders:
1. Definition and Core Concepts:
A Minimum Guaranteed Fill (MGF) order is a purchasing or fulfillment strategy where a supplier or retailer guarantees to fill at least a specified minimum quantity of an order, even if the full order quantity is not available in stock. This minimum quantity is pre-defined and agreed upon between the buyer and the seller. If the full order cannot be fulfilled, the seller is obligated to ship at least the MGF quantity, potentially backordering or expediting the remaining items. The primary goal of an MGF is to ensure a partial shipment is received, mitigating the risk of complete order failure.
The MGF percentage or quantity can vary based on factors like product availability, demand forecasting, lead times, and agreement between buyer and seller. A common example might be an MGF of 90%, meaning the seller guarantees to ship at least 90% of the ordered quantity.
2. Applications Across Industries:
MGFs find applications across numerous industries, with variations based on specific needs.
-
E-commerce: Online retailers utilize MGFs to ensure partial shipments are sent to customers, even if some items are out of stock. This reduces negative customer experiences associated with entirely delayed or cancelled orders. It allows for faster delivery of at least a portion of the order and maintains customer loyalty.
-
Manufacturing: Manufacturers use MGFs to ensure timely delivery of crucial components. Even if a supplier can't deliver the entire order, the MGF guarantees a minimum quantity, minimizing production disruptions and keeping assembly lines running.
-
Pharmaceuticals: The pharmaceutical industry utilizes MGFs to secure the supply of essential medicines. If a full order isn't immediately available, the MGF ensures a partial supply is delivered to meet urgent patient needs.
-
Wholesale Distribution: Wholesalers use MGFs to ensure retailers receive at least a portion of their orders, preventing stock-outs and maintaining consistent product availability.
3. Challenges and Solutions:
Implementing MGFs presents certain challenges:
-
Inventory Management: Accurate forecasting and efficient inventory management are crucial for effectively fulfilling MGF orders. Insufficient inventory can lead to increased costs and potentially failing to meet the MGF guarantee.
-
Order Processing: Efficient order processing systems are essential to manage partial shipments and backorders effectively. Complex systems are needed to track MGF quantities and communicate with customers about partial deliveries.
-
Communication: Clear communication between buyers and sellers is vital to avoid misunderstandings about MGF quantities, delivery times, and backordering processes.
-
Cost Management: MGFs can increase costs due to expediting or expedited shipping of partial orders. Careful planning and strategic inventory management are needed to mitigate these costs.
To address these challenges, businesses need to:
- Implement advanced inventory management systems: These systems utilize forecasting techniques and real-time inventory tracking to optimize stock levels and predict demand accurately.
- Invest in robust order management software: This software automates order processing, tracks partial shipments, manages backorders, and ensures effective communication with customers.
- Establish clear communication protocols: This involves developing standardized procedures for communicating MGF details to both internal teams and external partners.
- Develop strategies for cost optimization: This could involve negotiating favorable shipping rates, optimizing inventory levels, and strategically using different shipping options for partial shipments.
4. Impact on Innovation:
MGFs are driving innovation in supply chain management:
-
Predictive Analytics: Improved forecasting techniques leverage data analysis to predict demand more accurately, minimizing the likelihood of stockouts and ensuring that MGF guarantees can be met consistently.
-
Automation and Robotics: Automation and robotics are increasingly used in warehousing and distribution to enhance efficiency and ensure timely fulfillment of MGF orders.
-
AI-Powered Inventory Optimization: Artificial intelligence and machine learning are used to optimize inventory levels dynamically, adapting to fluctuating demand and reducing the risk of failing to meet MGF commitments.
Closing Insights: Summarizing the Core Discussion:
Minimum Guaranteed Fill orders are not merely a contractual obligation; they are a strategic tool for optimizing order fulfillment and enhancing customer satisfaction. By carefully considering the challenges and implementing the appropriate solutions, businesses can successfully leverage MGFs to improve their supply chain efficiency, enhance customer relationships, and gain a competitive advantage.
Exploring the Connection Between Order Processing Systems and Minimum Guaranteed Fill (MGF) Orders:
The relationship between order processing systems and MGF orders is pivotal. Effective order processing systems are fundamental to successfully implementing and managing MGFs. Without robust order management software, it becomes incredibly difficult to track partial shipments, manage backorders, and communicate effectively with customers regarding partially fulfilled orders. Efficient order processing software enables the automation of many crucial steps, reducing the risk of errors and improving overall efficiency.
Key Factors to Consider:
-
Roles and Real-World Examples: Order processing systems play a critical role in ensuring that the MGF quantity is accurately identified, flagged, and allocated for shipment. A company might use a system that prioritizes the MGF items for picking and packing, ensuring those items are shipped first.
-
Risks and Mitigations: Inadequate order processing systems can lead to delays in fulfilling the MGF portion of the order, potentially resulting in customer dissatisfaction and missed business opportunities. Investing in a system with automated alerts and real-time tracking can significantly reduce this risk.
-
Impact and Implications: The efficiency of the order processing system directly influences the speed and accuracy of MGF fulfillment. A well-integrated system can streamline the entire process, improving customer satisfaction and reducing operational costs.
Conclusion: Reinforcing the Connection:
The interplay between robust order processing systems and MGF orders is undeniable. Businesses that prioritize investment in advanced order management software are better positioned to successfully implement and manage MGFs, reaping the benefits of improved efficiency, enhanced customer satisfaction, and strengthened competitive positioning.
Further Analysis: Examining Order Management Software in Greater Detail:
Sophisticated order management software often incorporates features specifically designed to support MGF orders. These features can include:
-
Automated Allocation: The software automatically allocates the MGF quantity from available inventory, prioritizing its shipment.
-
Partial Shipment Management: The system seamlessly manages partial shipments, generating accurate shipping labels and tracking information.
-
Backorder Management: The software automatically creates and tracks backorders for items that are not part of the MGF quantity.
-
Real-Time Reporting and Analytics: The software provides real-time visibility into MGF order status, enabling proactive problem-solving and efficient resource allocation.
-
Customer Communication Tools: The system facilitates clear and timely communication with customers about partial shipments and backorders.
FAQ Section: Answering Common Questions About Minimum Guaranteed Fill Orders:
Q: What is a Minimum Guaranteed Fill (MGF) order?
A: An MGF order is an agreement where a supplier guarantees to ship at least a specified minimum quantity, even if the full order is unavailable.
Q: How is an MGF percentage determined?
A: The MGF percentage is negotiated between the buyer and seller, considering factors like product availability, demand forecasting, and lead times.
Q: What happens if the supplier cannot meet the MGF?
A: Failure to meet the MGF usually results in penalties as outlined in the agreement, potentially including financial compensation or expedited shipping of the remaining items.
Q: How do MGF orders impact customer satisfaction?
A: MGFs help ensure customers receive at least a portion of their order, minimizing the negative impact of stockouts and improving overall satisfaction.
Practical Tips: Maximizing the Benefits of MGF Orders:
-
Accurate Demand Forecasting: Use advanced forecasting techniques to improve inventory management and reduce the risk of stockouts.
-
Efficient Inventory Management: Implement robust inventory control systems to ensure accurate stock levels and facilitate timely order fulfillment.
-
Strategic Supplier Relationships: Build strong relationships with reliable suppliers who can consistently meet MGF commitments.
-
Flexible Order Processing System: Invest in a robust order management system that can handle partial shipments and backorders efficiently.
-
Clear Communication Protocols: Establish clear communication channels with both customers and suppliers to manage expectations effectively.
Final Conclusion: Wrapping Up with Lasting Insights:
Minimum Guaranteed Fill orders are a transformative element in modern supply chain management. By understanding their nuances, implementing best practices, and leveraging advanced technology, businesses can harness the power of MGFs to optimize their operations, improve customer satisfaction, and build a more resilient and competitive supply chain. The future of efficient order fulfillment rests on a clear comprehension and strategic implementation of this critical concept.
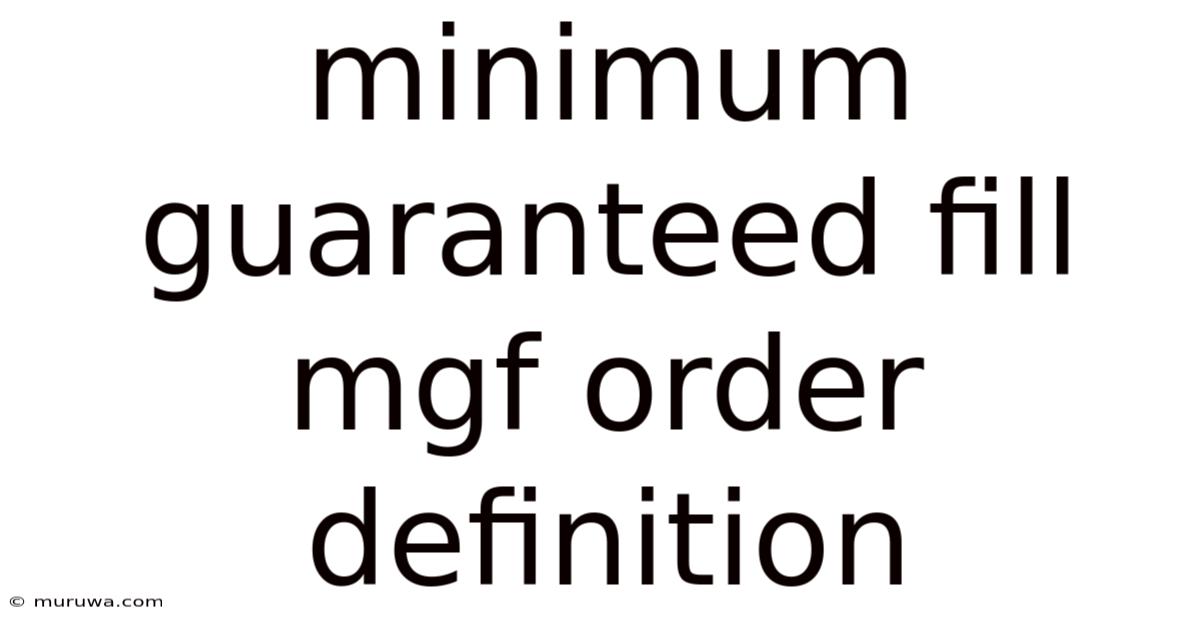
Thank you for visiting our website wich cover about Minimum Guaranteed Fill Mgf Order Definition. We hope the information provided has been useful to you. Feel free to contact us if you have any questions or need further assistance. See you next time and dont miss to bookmark.
Also read the following articles
Article Title | Date |
---|---|
What Does Asset Management Do | Apr 25, 2025 |
What Is A Liquid Capital Structure | Apr 25, 2025 |
What Role Do Information Asymmetries Taxes And Agency Costs Have In Capital Structure Theory | Apr 25, 2025 |
Moguls Definition Influence And Examples | Apr 25, 2025 |
Multi Index Option Definition | Apr 25, 2025 |