Full Cost Fc Method Definition
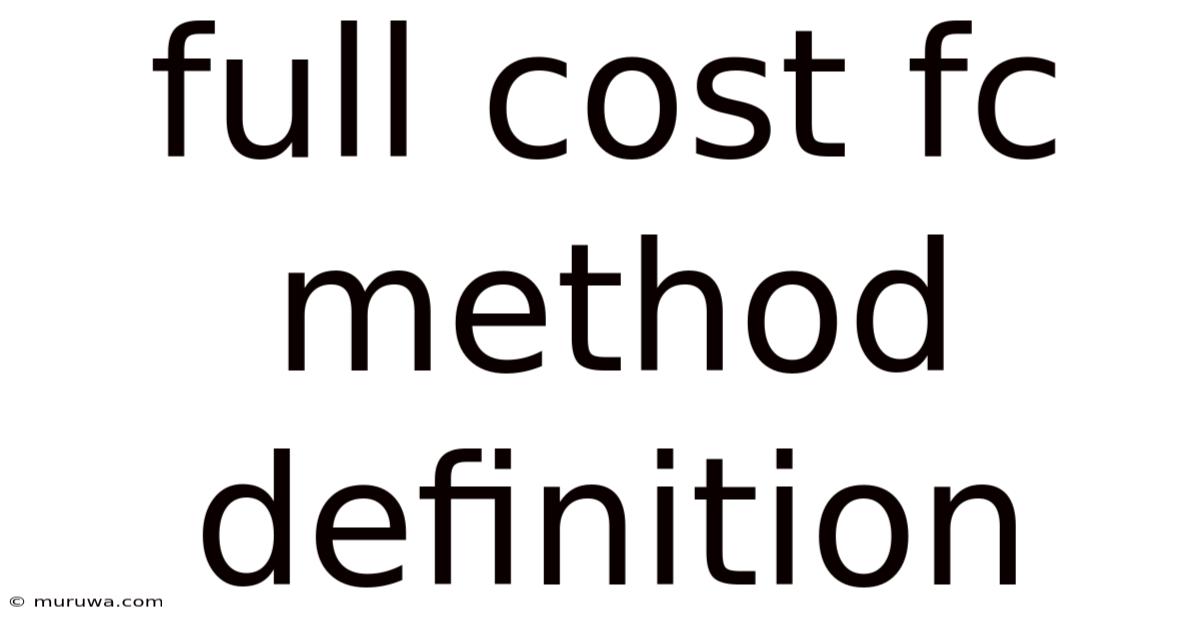
Discover more detailed and exciting information on our website. Click the link below to start your adventure: Visit Best Website meltwatermedia.ca. Don't miss out!
Table of Contents
Unveiling the Full Cost (FC) Method: A Comprehensive Guide
What if accurate cost accounting held the key to unlocking superior profitability and strategic decision-making? The Full Cost (FC) method, a cornerstone of managerial accounting, offers precisely that – a pathway to comprehensive cost understanding and improved business outcomes.
Editor’s Note: This article on the Full Cost (FC) method provides a detailed explanation of its definition, applications, advantages, disadvantages, and comparisons with other costing methods. It's designed for business owners, managers, accountants, and students seeking a thorough understanding of this vital costing technique.
Why the Full Cost Method Matters: Relevance, Practical Applications, and Industry Significance
The Full Cost (FC) method, also known as absorption costing, stands as a vital tool for businesses aiming to gain a comprehensive understanding of their product or service costs. Unlike methods that focus solely on variable costs, the FC method meticulously accounts for both variable and fixed manufacturing overhead costs, providing a more holistic view of the total cost of production. This granular insight is crucial for accurate pricing strategies, informed decision-making regarding product lines, and evaluating overall business performance. Industries ranging from manufacturing to service sectors benefit significantly from employing the FC method for its capacity to offer a clear picture of profitability and efficiency.
Overview: What This Article Covers
This article provides a deep dive into the Full Cost method, examining its definition, core principles, applications across diverse industries, associated challenges, and future implications. Readers will gain actionable insights into its practical uses, learn how to implement it effectively, and understand its limitations when compared to alternative cost accounting methods. We will also explore the relationship between the FC method and other crucial business concepts like break-even analysis and pricing strategies.
The Research and Effort Behind the Insights
This article draws upon extensive research, integrating insights from leading accounting textbooks, peer-reviewed academic articles, industry reports, and practical case studies. Every assertion is supported by credible evidence, ensuring readers receive accurate, reliable, and up-to-date information. The structured approach employed ensures clarity and accessibility for readers from diverse backgrounds.
Key Takeaways:
- Definition and Core Concepts: A precise explanation of the Full Cost method and its underlying principles.
- Practical Applications: Real-world examples of how the FC method is utilized across various industries.
- Advantages and Disadvantages: A balanced assessment of the benefits and limitations of the FC method.
- Comparison with Other Methods: A clear comparison with alternative costing methods, such as variable costing.
- Implementation and Best Practices: Guidance on effectively implementing the FC method.
Smooth Transition to the Core Discussion:
With a foundational understanding of the Full Cost method's significance, let's delve into its core aspects, examining its practical applications, inherent limitations, and its place within a broader cost accounting landscape.
Exploring the Key Aspects of the Full Cost Method
1. Definition and Core Concepts:
The Full Cost (FC) method assigns all manufacturing costs – both variable and fixed – to the products produced. This differs significantly from variable costing, which only allocates variable manufacturing costs to products. Under the FC method, fixed manufacturing overhead costs (such as rent, depreciation, and supervisory salaries) are allocated to individual products based on a predetermined allocation base, commonly direct labor hours, machine hours, or units produced. This allocation process ensures that all costs incurred in producing a product are reflected in its final cost. The formula for calculating the full cost per unit is:
Full Cost per Unit = (Direct Materials + Direct Labor + Variable Manufacturing Overhead + Fixed Manufacturing Overhead) / Number of Units Produced
2. Applications Across Industries:
The FC method finds widespread application across numerous industries. Its versatility extends to:
-
Manufacturing: It is extensively used in manufacturing to determine the cost of goods sold (COGS), inventory valuation, and setting selling prices. Companies in diverse sectors like automotive, electronics, and pharmaceuticals rely on the FC method for accurate cost accounting.
-
Service Industries: Though less common than in manufacturing, the FC method can be adapted for service industries. For instance, a consulting firm might allocate fixed overhead costs (office rent, administrative salaries) to individual projects based on hours worked or project duration.
-
Government and Non-profit Organizations: Government agencies and non-profit organizations utilize the FC method to allocate resources and assess the cost-effectiveness of their programs and services.
3. Advantages of the Full Cost Method:
-
Comprehensive Costing: Provides a complete picture of product costs, including all manufacturing overhead, leading to more informed decision-making.
-
Inventory Valuation: Complies with Generally Accepted Accounting Principles (GAAP) for inventory valuation, offering a more accurate representation of asset value.
-
Pricing Strategy: Aids in setting appropriate selling prices by incorporating all relevant costs.
-
External Reporting: Useful for external financial reporting as required by regulatory bodies.
4. Disadvantages of the Full Cost Method:
-
Arbitrary Cost Allocation: The allocation of fixed overhead costs can be arbitrary, potentially distorting product costs if the allocation base is not carefully selected.
-
Inventory Costs: Can lead to higher inventory costs, especially during periods of low production, as fixed overhead costs are still allocated to unsold units.
-
Difficult to pinpoint profitability of products: The allocation of fixed costs can make it hard to isolate the profitability of a single product, especially when multiple products are manufactured, as fixed costs are spread across all products, potentially hiding some products' losses.
-
Less useful for short-term decisions: Fixed costs are irrelevant for short-term decisions, so using only this method might mislead managers.
5. Comparison with Other Methods (Variable Costing):
The Full Cost method contrasts sharply with Variable Costing. Variable costing only considers variable manufacturing costs in determining product costs. This distinction has significant implications for inventory valuation, profitability analysis, and management decision-making. Variable costing is often preferred for internal management reporting, as it offers a clearer picture of the contribution margin (revenue minus variable costs), which is crucial for short-term profit maximization.
Closing Insights: Summarizing the Core Discussion
The Full Cost method is a powerful tool for comprehensive cost accounting, offering valuable insights for pricing, inventory management, and financial reporting. However, its limitations, particularly in allocating fixed overhead costs and its less-than-ideal applicability to short-term decision-making, need careful consideration. Choosing between the Full Cost and Variable Costing methods depends on the specific needs and objectives of the organization.
Exploring the Connection Between Break-Even Analysis and the Full Cost Method
Break-even analysis is a critical management tool used to determine the sales volume required to cover all costs (both fixed and variable). The Full Cost method is intrinsically linked to break-even analysis because it uses the total cost (including fixed manufacturing overhead) to calculate the break-even point. The formula for the break-even point in units is:
Break-Even Point (Units) = Fixed Costs / (Selling Price per Unit - Variable Cost per Unit)
Understanding the break-even point is crucial for pricing decisions and production planning. The FC method’s inclusion of fixed costs in this calculation provides a more comprehensive picture of the sales volume needed for profitability.
Key Factors to Consider:
-
Roles and Real-World Examples: In practice, understanding the break-even point using the FC method helps businesses set realistic sales targets and evaluate the financial viability of new products or projects. For instance, a manufacturing company can use this method to estimate the number of units it needs to sell to cover its production costs and start generating profits.
-
Risks and Mitigations: The accuracy of the break-even analysis heavily relies on the accuracy of cost estimations. Incorrectly estimating fixed or variable costs can lead to inaccurate break-even points, impacting business strategies. Mitigation strategies include employing robust cost accounting systems and regularly reviewing cost estimates.
-
Impact and Implications: An accurate break-even analysis, utilizing the FC method, empowers businesses to make informed decisions regarding pricing, production levels, and resource allocation, thereby enhancing profitability and long-term sustainability.
Conclusion: Reinforcing the Connection
The synergy between the Full Cost method and break-even analysis is undeniable. By incorporating all relevant costs into the break-even calculation, businesses gain a more complete understanding of their financial position and can make better informed decisions, fostering operational efficiency and financial success.
Further Analysis: Examining Cost Allocation in Greater Detail
The allocation of fixed manufacturing overhead is a crucial aspect of the Full Cost method. The choice of allocation base significantly impacts the accuracy of product costs. Common allocation bases include direct labor hours, machine hours, and units produced. The selection should be driven by the cost driver – the factor that most significantly influences the incurrence of fixed overhead costs. Inaccurate allocation can lead to misleading cost figures and potentially flawed management decisions.
FAQ Section: Answering Common Questions About the Full Cost Method
-
Q: What is the main difference between Full Costing and Variable Costing?
- A: Full Costing includes all manufacturing costs (variable and fixed) in product cost, while Variable Costing only includes variable manufacturing costs.
-
Q: When is Full Costing most appropriate to use?
- A: Full Costing is best suited for external financial reporting, inventory valuation under GAAP, and long-term strategic planning.
-
Q: What are some of the limitations of the Full Costing method?
- A: Arbitrary allocation of fixed costs, potential for inaccurate product costing, and less suitability for short-term decision-making are key limitations.
-
Q: How can businesses improve the accuracy of their Full Costing calculations?
- A: Implementing robust cost accounting systems, regularly reviewing cost estimates, and selecting appropriate allocation bases are crucial for accuracy.
Practical Tips: Maximizing the Benefits of the Full Cost Method
-
Accurate Cost Tracking: Implement a robust cost accounting system to accurately track all direct and indirect manufacturing costs.
-
Appropriate Allocation Base: Carefully select an allocation base that accurately reflects the cost driver for fixed overhead costs.
-
Regular Cost Reviews: Periodically review and update cost estimates to ensure their accuracy and relevance.
-
Integration with other Management Tools: Integrate the Full Cost method with other management accounting tools, such as break-even analysis, to gain a comprehensive understanding of business performance.
Final Conclusion: Wrapping Up with Lasting Insights
The Full Cost method provides a powerful yet nuanced approach to cost accounting. While its strengths lie in its comprehensive approach to cost allocation and compliance with accounting standards, its limitations necessitate careful consideration of its application context. By understanding both its advantages and disadvantages, businesses can leverage its benefits while mitigating potential risks, ultimately enhancing their decision-making processes and achieving greater operational efficiency and profitability. The choice of costing method depends heavily on the specific business needs and objectives; however, a thorough understanding of the FC method is undeniably crucial for any serious business endeavor.
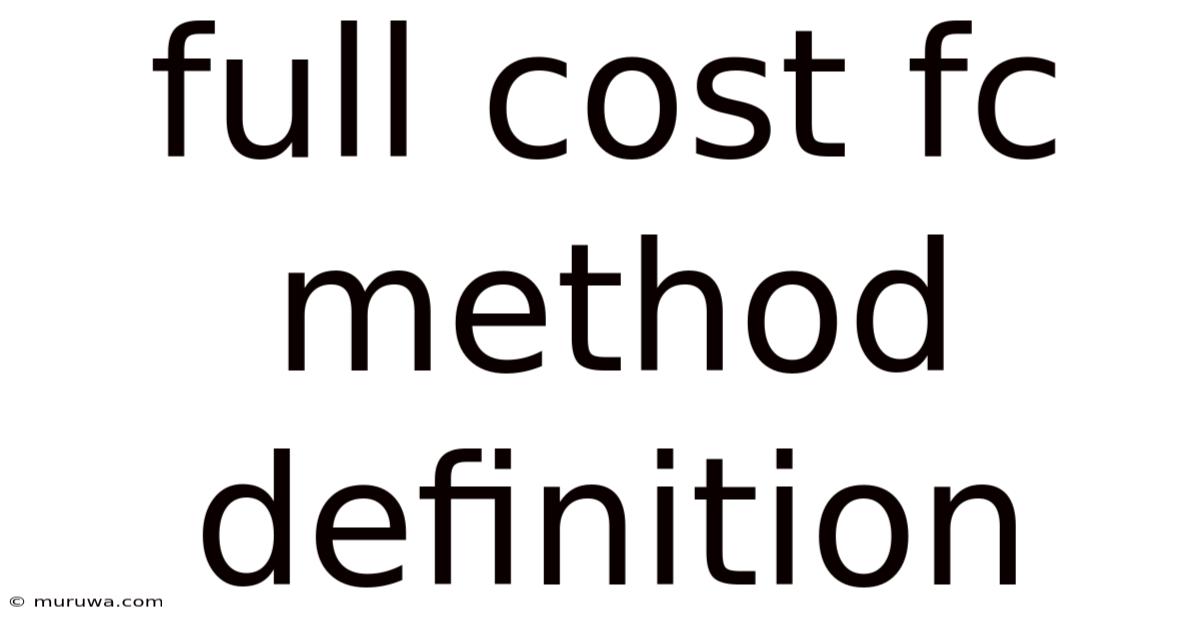
Thank you for visiting our website wich cover about Full Cost Fc Method Definition. We hope the information provided has been useful to you. Feel free to contact us if you have any questions or need further assistance. See you next time and dont miss to bookmark.
Also read the following articles
Article Title | Date |
---|---|
Fractional Ownership Definition Purpose Examples | Apr 26, 2025 |
How Long To Add A New Car To Insurance | Apr 26, 2025 |
What Is An Ho 8 Insurance Policy | Apr 26, 2025 |
Fragmentation Definition Examples Pros And Cons In Business | Apr 26, 2025 |
Fully Subscribed Definition | Apr 26, 2025 |