Flexible Manufacturing System Fms Definition And How It Works
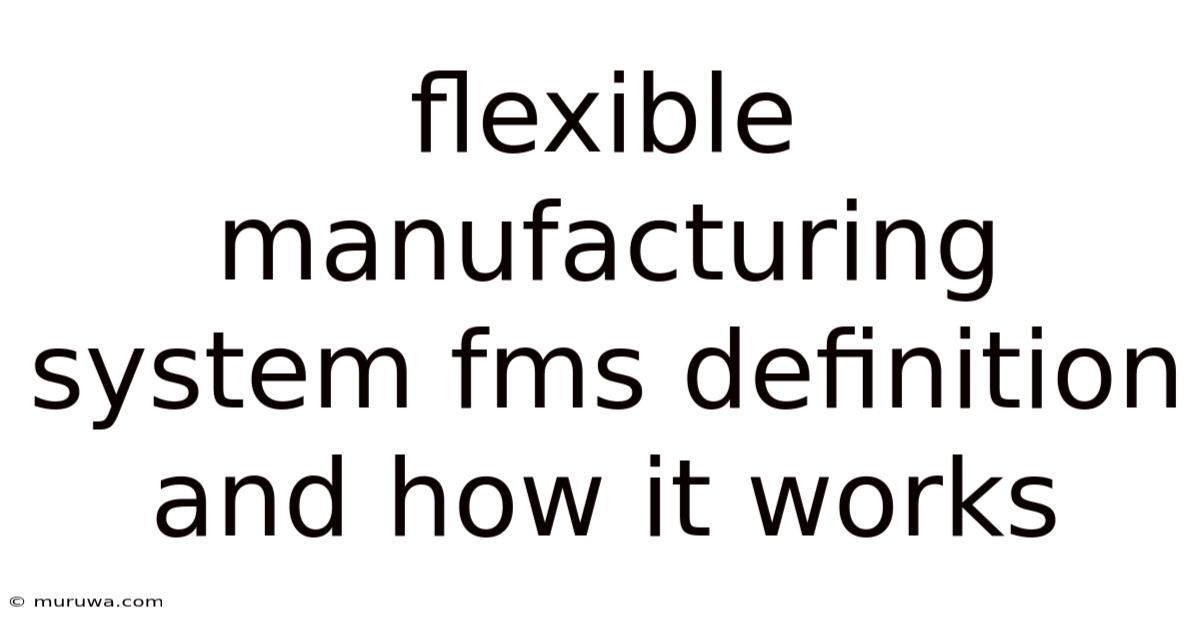
Discover more detailed and exciting information on our website. Click the link below to start your adventure: Visit Best Website meltwatermedia.ca. Don't miss out!
Table of Contents
Unleashing the Power of Flexibility: A Deep Dive into Flexible Manufacturing Systems (FMS)
What if the future of manufacturing lies in systems that adapt seamlessly to changing demands? Flexible Manufacturing Systems (FMS) are revolutionizing how industries produce goods, offering unprecedented agility and efficiency.
Editor’s Note: This article on Flexible Manufacturing Systems (FMS) provides a comprehensive overview of this transformative technology, exploring its definition, workings, benefits, challenges, and future implications. Updated insights ensure readers gain a current understanding of FMS and its impact on modern manufacturing.
Why Flexible Manufacturing Systems Matter:
In today's dynamic global marketplace, businesses face increasing pressure to deliver customized products quickly and cost-effectively. Consumer preferences shift rapidly, and competition is fierce. Traditional manufacturing methods, often rigid and inflexible, struggle to keep pace. This is where Flexible Manufacturing Systems (FMS) emerge as a game-changer. FMS allows manufacturers to respond swiftly to changing market demands, produce diverse product lines with minimal setup time, and significantly improve overall efficiency. This adaptability translates to reduced costs, increased profitability, and a stronger competitive edge. FMS is crucial for industries requiring high product variety, short production runs, and rapid response to market fluctuations – from automotive and electronics to aerospace and pharmaceuticals.
Overview: What This Article Covers:
This article will provide a detailed exploration of FMS, covering its definition, core components, operational principles, advantages and disadvantages, implementation strategies, and future trends. We'll examine real-world examples and address common challenges associated with FMS adoption. Readers will gain a thorough understanding of this powerful technology and its potential to reshape manufacturing landscapes.
The Research and Effort Behind the Insights:
This article draws on extensive research, integrating insights from leading academic publications, industry reports, case studies of successful FMS implementations, and interviews with experts in manufacturing technology. The information presented is rigorously vetted to ensure accuracy and provide readers with a reliable and up-to-date resource.
Key Takeaways:
- Definition and Core Concepts: A clear understanding of FMS and its foundational elements.
- Components and Architecture: Detailed explanation of the essential parts of an FMS.
- Operational Principles: How FMS utilizes automation and control systems for flexibility.
- Advantages and Disadvantages: A balanced perspective of the benefits and drawbacks.
- Implementation Strategies: Guidance on successful FMS adoption and integration.
- Future Trends and Implications: Exploring the evolving landscape of FMS technology.
Smooth Transition to the Core Discussion:
Having established the importance of FMS, let's delve into a detailed examination of its core components, operational principles, and practical applications within various industries.
Exploring the Key Aspects of Flexible Manufacturing Systems:
1. Definition and Core Concepts:
A Flexible Manufacturing System (FMS) is a highly automated manufacturing process characterized by its ability to efficiently produce a variety of products with minimal setup time. Unlike traditional assembly lines dedicated to a single product, FMS utilizes computer-controlled machines, automated material handling systems, and sophisticated software to manage and optimize the entire production process. This flexibility allows manufacturers to adapt quickly to changing order volumes, product designs, and market demands. The key characteristic is the ability to switch between different products without significant downtime or retooling.
2. Components and Architecture:
A typical FMS comprises several interconnected components:
- Computer Numerical Control (CNC) Machines: These programmable machines perform various manufacturing operations, such as milling, turning, drilling, and grinding. Their flexibility allows them to handle diverse parts and operations.
- Automated Guided Vehicles (AGVs) or Robots: These systems handle the movement of materials and workpieces between different machines, eliminating manual handling and minimizing delays.
- Automated Storage and Retrieval Systems (AS/RS): These systems store raw materials, work-in-progress, and finished goods efficiently, ensuring timely access to components.
- Centralized Control System: A sophisticated computer system orchestrates the entire FMS, managing the flow of materials, scheduling production, monitoring machine performance, and controlling the entire manufacturing process. This system uses sophisticated software algorithms to optimize resource allocation and minimize lead times.
- Supervisory Control and Data Acquisition (SCADA) System: This system monitors the real-time performance of the entire FMS, collecting data from various sensors and providing valuable insights into efficiency and potential bottlenecks.
These components work in concert, creating a highly coordinated and responsive production environment. The architecture is often cell-based, with groups of machines dedicated to specific operations or product families. This cellular structure enhances efficiency and simplifies control.
3. Operational Principles:
FMS relies on several key operational principles:
- Computer-Integrated Manufacturing (CIM): The entire manufacturing process is integrated through a computer system, enabling seamless data flow, optimized scheduling, and real-time monitoring.
- Programmable Logic Controllers (PLCs): These controllers automate individual machine functions and coordinate their operation within the larger FMS.
- Automated Material Handling: The use of AGVs, robots, or conveyor systems ensures efficient movement of materials and minimizes manual intervention.
- Flexible Routing: Workpieces can be routed through different machines based on their specific requirements, providing flexibility in production sequences.
- Real-Time Monitoring and Control: The centralized control system monitors machine performance, detects errors, and adjusts the production process as needed.
4. Advantages of FMS:
- Increased Flexibility: The ability to easily switch between different products and adjust production volumes.
- Improved Efficiency: Reduced setup times, optimized production flows, and minimized waste.
- Enhanced Productivity: Higher output rates due to automation and optimized resource utilization.
- Reduced Lead Times: Faster production cycles, enabling quicker delivery to customers.
- Improved Product Quality: Consistent and precise manufacturing processes minimize defects.
- Lower Labor Costs: Automation reduces the need for manual labor.
- Better Inventory Management: Efficient storage and retrieval systems minimize inventory holding costs.
5. Disadvantages of FMS:
- High Initial Investment: The cost of implementing an FMS can be significant.
- Complexity: Designing, implementing, and maintaining an FMS requires specialized expertise.
- Integration Challenges: Integrating different components and systems can be complex.
- Potential for Downtime: Malfunctions in any component can disrupt the entire production process.
- Need for Skilled Personnel: Operating and maintaining an FMS requires skilled technicians and programmers.
- Dependence on Technology: Reliability and efficiency are dependent on the performance of the technology involved.
6. Implementation Strategies:
Successful FMS implementation requires careful planning and execution:
- Needs Assessment: Clearly define production requirements and objectives.
- System Design: Develop a detailed design that meets specific needs and integrates seamlessly with existing systems.
- Vendor Selection: Choose reliable vendors capable of providing quality components and support.
- Training: Train personnel on the operation and maintenance of the FMS.
- Testing and Commissioning: Thoroughly test and commission the system to ensure proper functionality.
- Continuous Improvement: Monitor performance and make adjustments to optimize efficiency over time.
7. Impact on Innovation:
FMS has profoundly impacted innovation in manufacturing by fostering:
- Lean Manufacturing Principles: FMS encourages the elimination of waste and the optimization of production processes.
- Mass Customization: The ability to produce customized products efficiently at scale.
- Digital Twins: Virtual representations of FMS systems allow for simulation and optimization before actual implementation.
- Predictive Maintenance: Data analytics help anticipate and prevent equipment failures, minimizing downtime.
Exploring the Connection Between Data Analytics and Flexible Manufacturing Systems:
Data analytics plays a pivotal role in maximizing the benefits of FMS. The vast amounts of data generated by an FMS provide invaluable insights into operational efficiency, potential bottlenecks, and opportunities for improvement. By analyzing this data, manufacturers can:
Roles and Real-World Examples:
- Predictive Maintenance: Analyzing sensor data from machines can predict potential failures, allowing for preventative maintenance and minimizing downtime. For example, a car manufacturer using FMS can predict when a specific robotic arm needs servicing, preventing production delays.
- Optimized Scheduling: Data analysis can optimize production schedules, ensuring efficient resource allocation and minimizing lead times. A pharmaceutical company using FMS can optimize drug production schedules based on real-time demand and material availability.
- Quality Control: Analyzing data on product defects can identify sources of errors and improve quality control processes. An electronics manufacturer can identify which stage of the FMS is producing the most defects, allowing targeted improvements.
Risks and Mitigations:
- Data Security: Protecting sensitive data from unauthorized access and cyberattacks is crucial. Strong cybersecurity measures are needed to mitigate this risk.
- Data Integration Challenges: Integrating data from various sources can be complex. Standardization of data formats and protocols is vital.
- Lack of Expertise: Analyzing and interpreting data requires skilled personnel. Investing in training and development is essential.
Impact and Implications:
The use of data analytics in FMS enhances efficiency, reduces costs, and improves overall productivity. It also enables manufacturers to respond more effectively to changing market demands and maintain a competitive edge.
Conclusion: Reinforcing the Connection:
The interplay between data analytics and FMS is synergistic. Data analytics transforms FMS from a complex automated system into an intelligent and self-optimizing production environment. By harnessing the power of data, manufacturers can realize the full potential of FMS and achieve significant improvements in efficiency, quality, and profitability.
Further Analysis: Examining Data Analytics in Greater Detail:
The application of Artificial Intelligence (AI) and Machine Learning (ML) within data analytics is further enhancing the capabilities of FMS. AI-powered systems can identify patterns and anomalies in data that might be missed by human analysts, leading to more effective predictive maintenance, optimized scheduling, and improved quality control. Moreover, AI can assist in the design and optimization of FMS, simulating different scenarios and identifying the most efficient configurations.
FAQ Section: Answering Common Questions About FMS:
- What is the ROI of implementing an FMS? The ROI varies greatly depending on the specific industry, the scale of the system, and the efficiency improvements achieved. However, successful FMS implementations often yield significant returns through increased productivity, reduced costs, and improved product quality.
- How long does it take to implement an FMS? Implementation timelines vary, but it typically takes several months to several years, depending on the complexity of the system and the integration requirements.
- What are the key challenges in maintaining an FMS? Maintaining an FMS requires specialized expertise and ongoing investments in equipment upgrades and software maintenance. Downtime due to equipment malfunctions is also a significant concern.
Practical Tips: Maximizing the Benefits of FMS:
- Start Small: Begin with a pilot project to test the feasibility of FMS before investing in a large-scale system.
- Focus on Integration: Ensure seamless integration between different components and systems.
- Invest in Training: Train personnel thoroughly to operate and maintain the FMS effectively.
- Monitor Performance: Continuously monitor performance and make adjustments to optimize efficiency.
Final Conclusion: Wrapping Up with Lasting Insights:
Flexible Manufacturing Systems represent a transformative force in the manufacturing industry, enabling unprecedented levels of flexibility, efficiency, and productivity. By understanding their capabilities, challenges, and implementation strategies, manufacturers can harness the power of FMS to achieve significant competitive advantages in today’s dynamic global marketplace. The integration of advanced technologies like data analytics and AI will further enhance the capabilities of FMS, driving innovation and shaping the future of manufacturing.
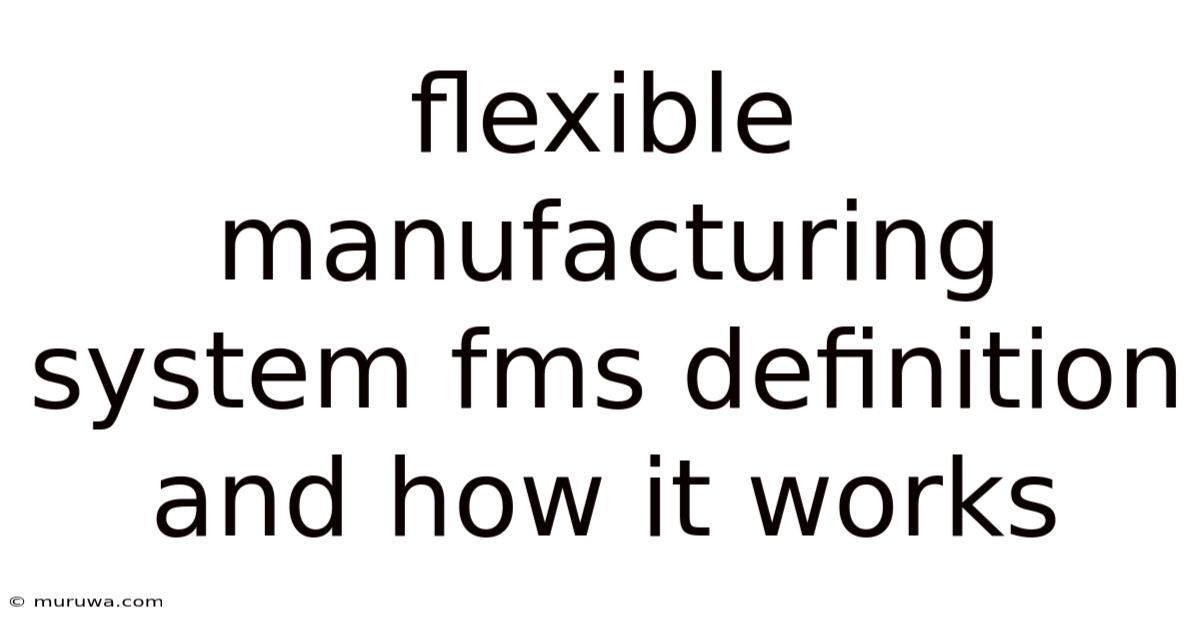
Thank you for visiting our website wich cover about Flexible Manufacturing System Fms Definition And How It Works. We hope the information provided has been useful to you. Feel free to contact us if you have any questions or need further assistance. See you next time and dont miss to bookmark.
Also read the following articles
Article Title | Date |
---|---|
What Is A Bailout Definition How They Work And Example | Apr 13, 2025 |
How Many Early Bird Check In Southwest Credit Card | Apr 13, 2025 |
What Is Backward Induction Definition How It Works And Example | Apr 13, 2025 |
What Happens If You Dont Use Insurance Money For Repairs Reddit | Apr 13, 2025 |
Bancassurance Definition | Apr 13, 2025 |