Carrying Costs Definition Types And Calculation Example
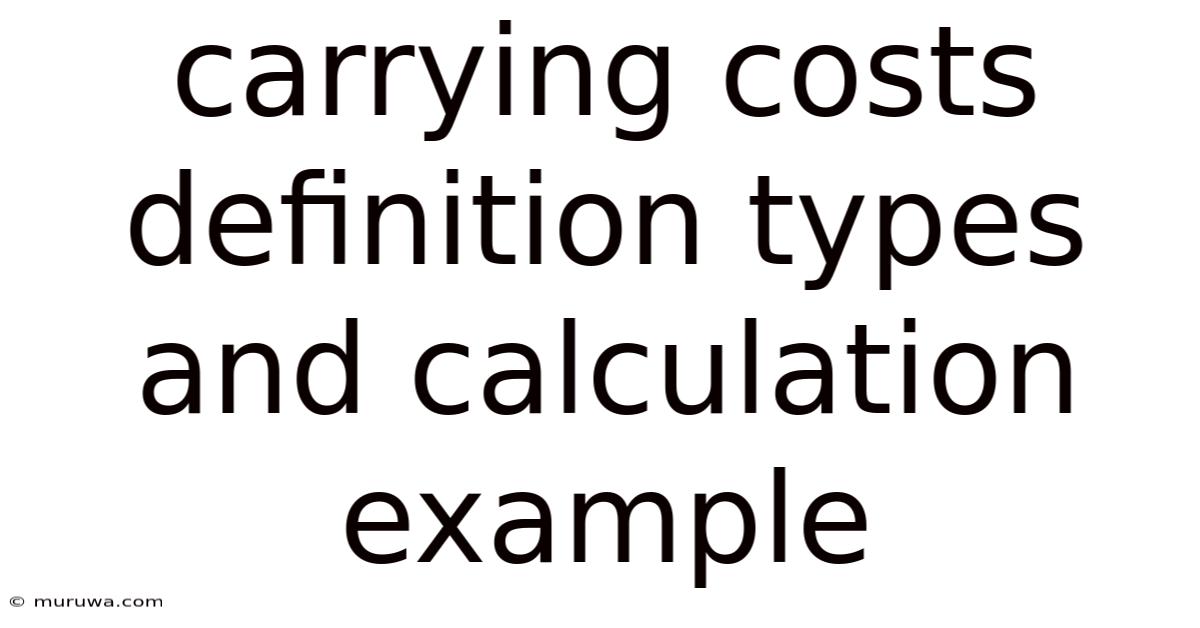
Discover more detailed and exciting information on our website. Click the link below to start your adventure: Visit Best Website meltwatermedia.ca. Don't miss out!
Table of Contents
Understanding Carrying Costs: Definition, Types, and Calculation Examples
What if a significant portion of your business's profitability hinges on effectively managing something as seemingly mundane as carrying costs? Optimizing these costs is crucial for maintaining a healthy bottom line and achieving sustainable growth.
Editor’s Note: This article on carrying costs provides a comprehensive overview of their definition, types, calculation, and practical applications. It's designed to help businesses of all sizes better understand and manage this often-overlooked aspect of their operations. Updated [Date].
Why Carrying Costs Matter:
Carrying costs, also known as holding costs or inventory holding costs, represent the total cost of storing and maintaining inventory. These costs are directly tied to the amount of inventory a business holds. While having sufficient inventory is essential for meeting customer demand, excessive inventory can severely impact profitability. Understanding and minimizing these costs is vital for optimizing supply chain efficiency, improving cash flow, and enhancing overall business performance. Ignoring these costs can lead to reduced profits, wasted resources, and potential business failure. The effective management of carrying costs impacts everything from pricing strategies to sales forecasting.
Overview: What This Article Covers:
This article provides a detailed examination of carrying costs, covering their definition, various types, and methods for calculation. Real-world examples will illustrate the practical application of these calculations, and the article will explore strategies for minimizing carrying costs and improving overall business efficiency.
The Research and Effort Behind the Insights:
This comprehensive guide draws upon established accounting principles, supply chain management literature, and practical business case studies. The information presented is supported by reputable sources and aims to provide readers with actionable insights for effective inventory management.
Key Takeaways:
- Definition and Core Concepts: A precise understanding of what constitutes carrying costs.
- Types of Carrying Costs: Detailed breakdown of the various cost components.
- Calculation Methods: Step-by-step procedures for accurately calculating carrying costs.
- Real-World Examples: Illustrative scenarios demonstrating the application of carrying cost calculations.
- Minimizing Carrying Costs: Practical strategies for reducing inventory holding expenses.
- Impact on Profitability: The direct correlation between carrying costs and profit margins.
Smooth Transition to the Core Discussion:
Now that the importance of carrying costs is established, let's delve into a detailed exploration of their various components, calculation methods, and effective management strategies.
Exploring the Key Aspects of Carrying Costs:
1. Definition and Core Concepts:
Carrying costs represent the total expenses associated with holding inventory. These costs are incurred from the time inventory is acquired until it is sold. They are distinct from ordering costs (the costs associated with placing an order) and stockout costs (the costs incurred when inventory runs out). Efficiently managing carrying costs is a cornerstone of effective inventory management.
2. Types of Carrying Costs:
Carrying costs encompass a range of expenses, which can be broadly categorized as follows:
-
Storage Costs: This is often the most significant component and includes rent or mortgage payments for warehouse space, utilities (electricity, heating, cooling), security systems, and insurance premiums for the warehouse and its contents. Consider also the cost of racking and shelving systems.
-
Insurance Costs: Protecting inventory against theft, damage, or loss requires insurance coverage. The premium paid for this insurance contributes directly to carrying costs.
-
Taxes: Property taxes levied on the warehouse and inventory itself contribute to the overall holding cost. Some jurisdictions may impose additional taxes specifically on stored goods.
-
Obsolescence Costs: Products become obsolete due to technological advancements, changing consumer preferences, or expiration dates (especially relevant for perishable goods). This cost represents the loss in value of inventory that can no longer be sold at its original price, or at all.
-
Depreciation Costs: For some inventory items, the value depreciates over time, even if not obsolete. This is particularly true for specialized equipment or technology.
-
Waste Costs: This includes spoilage, damage, or theft of inventory. Effective warehouse management can help mitigate this cost.
-
Capital Costs: This represents the opportunity cost of tying up capital in inventory. The money invested in inventory could have been used elsewhere, such as investing in other business ventures, paying down debt, or increasing marketing efforts. This is often calculated as a percentage of the inventory's value.
-
Handling Costs: These are the costs associated with moving inventory within the warehouse, including labor costs for forklift operators, stock handlers, and other personnel.
3. Calculation Methods:
Calculating carrying costs involves summing the various cost components. A common approach involves expressing the total carrying cost as a percentage of the average inventory value. The formula is:
Carrying Cost Percentage = (Total Carrying Costs / Average Inventory Value) * 100
Average Inventory Value: This is calculated as (Beginning Inventory + Ending Inventory) / 2. A more sophisticated approach might use a weighted average based on inventory levels throughout the period.
Total Carrying Costs: This is the sum of all the cost components outlined above.
4. Real-World Examples:
Example 1: A Retail Business
Let's consider a retail business with an average inventory value of $100,000. Its carrying costs include:
- Storage Costs: $5,000 per year
- Insurance Costs: $1,000 per year
- Taxes: $500 per year
- Obsolescence Costs: $2,000 per year
- Capital Costs (20% of inventory value): $20,000 per year
Total Carrying Costs = $5,000 + $1,000 + $500 + $2,000 + $20,000 = $28,500
Carrying Cost Percentage = ($28,500 / $100,000) * 100 = 28.5%
Example 2: A Manufacturing Company
A manufacturing company has an average inventory value of $500,000. Its carrying costs are:
- Storage Costs: $15,000
- Insurance Costs: $3,000
- Taxes: $1,000
- Obsolescence Costs: $5,000
- Depreciation: $2,000
- Handling Costs: $4,000
- Capital Costs (15% of inventory value): $75,000
Total Carrying Costs = $15,000 + $3,000 + $1,000 + $5,000 + $2,000 + $4,000 + $75,000 = $105,000
Carrying Cost Percentage = ($105,000 / $500,000) * 100 = 21%
5. Minimizing Carrying Costs:
Several strategies can help businesses minimize their carrying costs:
-
Just-in-Time (JIT) Inventory Management: This approach minimizes inventory levels by receiving goods only when needed, thereby reducing storage and obsolescence costs.
-
Improved Forecasting: Accurate sales forecasting helps businesses order only the necessary inventory, reducing excess stock.
-
Efficient Warehouse Management: Optimizing warehouse layout and utilizing technology (e.g., warehouse management systems) improves inventory handling and minimizes waste.
-
Improved Inventory Control: Implementing robust inventory tracking systems minimizes losses due to theft or damage.
-
Negotiating Better Rates: Negotiating lower rates with suppliers, warehouse providers, and insurance companies can significantly impact carrying costs.
-
Product Diversification: Reducing reliance on a single product or a small number of products mitigates the risk of obsolescence.
6. Impact on Profitability:
High carrying costs directly impact a company's profitability by reducing profit margins. By effectively managing these costs, businesses can improve their overall financial performance.
Exploring the Connection Between Inventory Turnover and Carrying Costs:
Inventory turnover is a key metric that reflects how efficiently a company manages its inventory. It's calculated as Cost of Goods Sold / Average Inventory. A higher inventory turnover rate indicates that inventory is being sold quickly, minimizing the time it spends in storage and, therefore, reducing carrying costs. Conversely, a low inventory turnover rate suggests excessive inventory, leading to increased carrying costs and potentially impacting profitability.
Key Factors to Consider:
-
Roles and Real-World Examples: Companies with high inventory turnover rates (e.g., fast-fashion retailers) generally have lower carrying costs relative to their inventory value than companies with low inventory turnover (e.g., manufacturers of heavy machinery).
-
Risks and Mitigations: Failure to manage carrying costs can lead to significant financial losses, impacting cash flow and profitability. Strategies like JIT and improved forecasting mitigate these risks.
-
Impact and Implications: The impact of carrying costs extends beyond immediate financial implications. Excessive inventory can tie up capital, hindering business expansion and investment opportunities.
Conclusion: Reinforcing the Connection:
The relationship between inventory turnover and carrying costs is undeniable. Efficient inventory management, leading to a higher turnover rate, directly contributes to lower carrying costs and improved profitability. A proactive approach to managing these costs is essential for achieving long-term business success.
Further Analysis: Examining Inventory Turnover in Greater Detail:
Inventory turnover can be analyzed further by breaking it down by product category or product line. This allows businesses to identify specific areas where inventory management is inefficient and focus efforts on improving turnover rates in those areas. This granular analysis allows for more targeted interventions to reduce carrying costs.
FAQ Section: Answering Common Questions About Carrying Costs:
-
Q: What is the ideal carrying cost percentage? A: There's no single ideal percentage; it varies by industry and business model. A lower percentage generally indicates better efficiency.
-
Q: How often should carrying costs be calculated? A: Ideally, carrying costs should be calculated regularly, at least monthly or quarterly, to monitor trends and identify potential issues.
-
Q: Can I ignore carrying costs if my business is small? A: No, even small businesses need to be mindful of carrying costs. These costs can significantly impact profitability, regardless of business size.
-
Q: How can I estimate obsolescence costs? A: This requires analyzing historical data on product sell-through rates, considering factors like product lifecycle and market trends.
-
Q: What software can help me manage carrying costs? A: Several Enterprise Resource Planning (ERP) systems and inventory management software packages provide tools for tracking and analyzing inventory and associated costs.
Practical Tips: Maximizing the Benefits of Effective Carrying Cost Management:
- Regularly review inventory levels: Identify slow-moving items and consider strategies for clearing them.
- Implement a robust inventory tracking system: Use barcodes, RFID, or other technologies to improve accuracy and reduce manual errors.
- Negotiate with suppliers for better payment terms: This can improve cash flow and reduce the need to hold large quantities of inventory.
- Invest in warehouse optimization: Improve layout, storage, and handling to minimize costs and waste.
- Regularly review your forecasting methods: Identify areas for improvement to reduce forecast errors and excess inventory.
Final Conclusion: Wrapping Up with Lasting Insights:
Effectively managing carrying costs is not merely a cost-cutting exercise; it's a strategic imperative for businesses seeking sustainable profitability and growth. By understanding the various components of carrying costs, employing appropriate calculation methods, and implementing effective management strategies, businesses can significantly improve their bottom line and achieve a competitive advantage in the marketplace. The key is consistent monitoring, proactive adjustments, and a commitment to optimizing inventory management practices.
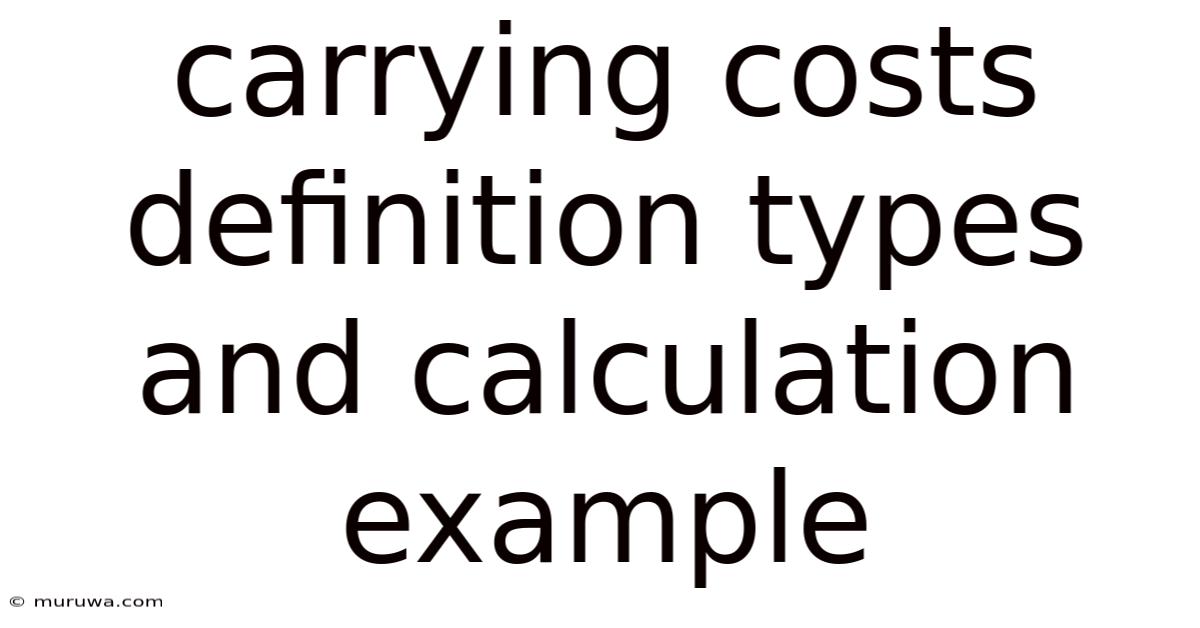
Thank you for visiting our website wich cover about Carrying Costs Definition Types And Calculation Example. We hope the information provided has been useful to you. Feel free to contact us if you have any questions or need further assistance. See you next time and dont miss to bookmark.
Also read the following articles
Article Title | Date |
---|---|
Car Title Loan Defined | Mar 11, 2025 |
Capital Accumulation Definition And How To Measure | Mar 11, 2025 |
How To Boost Credit Score While In Chapter 13 | Mar 11, 2025 |
Capital Decay Definition | Mar 11, 2025 |
How To Withdraw From Blockchain | Mar 11, 2025 |