Breakage Definition
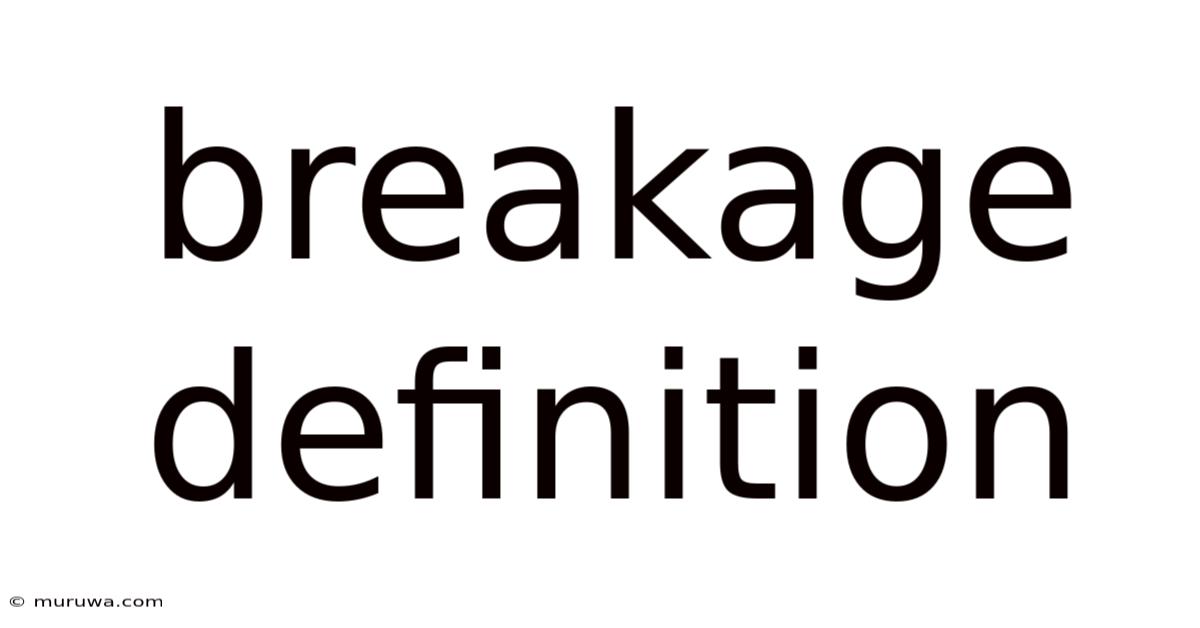
Discover more detailed and exciting information on our website. Click the link below to start your adventure: Visit Best Website meltwatermedia.ca. Don't miss out!
Table of Contents
Unraveling the Enigma of Breakage: A Comprehensive Guide
What if the seemingly simple concept of breakage holds the key to understanding complex systems and optimizing performance across diverse fields? Breakage, far from being a mere accident, is a phenomenon with profound implications, influencing everything from material science to economic models.
Editor’s Note: This article on breakage definition and its multifaceted implications has been published today, providing readers with the most up-to-date insights into this critical subject.
Why Breakage Matters: Relevance, Practical Applications, and Industry Significance
Breakage, in its broadest sense, refers to the separation of a material or system into multiple parts due to the application of force, stress, or other factors. While seemingly straightforward, the concept encompasses a wide array of phenomena with significant consequences across numerous industries. Understanding breakage is crucial for optimizing manufacturing processes, enhancing product durability, predicting failures, and mitigating risks in various applications. From the microscopic fracture of a single crystal to the catastrophic failure of a large-scale structure, breakage impacts efficiency, safety, and economic viability. This necessitates a deep understanding of its causes, mechanisms, and potential mitigation strategies. The impact of breakage extends to fields like materials science, engineering, economics (e.g., supply chain disruptions), and even biology (e.g., bone fracture).
Overview: What This Article Covers
This article provides a comprehensive exploration of breakage, moving beyond a simple definition to delve into its various manifestations and underlying causes. It examines the different types of breakage, the factors influencing it, and the methods used to characterize and predict it. We'll explore breakage in diverse contexts, from the microscopic world of materials science to the macroscopic scale of engineering structures. The article concludes with practical implications and future directions in breakage research.
The Research and Effort Behind the Insights
This article is the result of extensive research, drawing upon peer-reviewed scientific publications, engineering handbooks, industry reports, and case studies. The information presented is meticulously cross-referenced to ensure accuracy and reliability. The structured approach adopted allows for a systematic examination of the complexities of breakage, delivering clear and actionable insights.
Key Takeaways:
- Definition and Core Concepts: A thorough explanation of breakage encompassing its diverse forms and underlying mechanisms.
- Types of Breakage: Categorization of breakage based on material properties, loading conditions, and failure modes.
- Factors Influencing Breakage: Identification and analysis of variables contributing to the likelihood and severity of breakage.
- Characterization and Prediction: Examination of techniques used to quantify and forecast breakage in various contexts.
- Mitigation and Prevention: Exploration of strategies to reduce or eliminate breakage events.
- Real-world Applications: Case studies demonstrating the significance of breakage across diverse industries.
Smooth Transition to the Core Discussion
Having established the importance of understanding breakage, let’s now delve into a more detailed analysis, exploring its various facets and implications.
Exploring the Key Aspects of Breakage
1. Definition and Core Concepts:
Breakage, in the context of materials science and engineering, signifies the irreversible separation of a solid material into two or more pieces under the influence of external forces or internal stresses. This separation can occur along pre-existing flaws or initiate at stress concentration points. The type of breakage depends heavily on the material's properties (ductility, brittleness, strength), the nature of the applied load (tensile, compressive, shear, fatigue), and the environment (temperature, humidity).
2. Types of Breakage:
Breakage can be broadly categorized into:
- Brittle Fracture: Characterized by sudden, catastrophic failure with little or no plastic deformation. This type of breakage is typical of ceramic materials, glass, and some metals under specific conditions. The fracture surfaces are often smooth and planar.
- Ductile Fracture: Involves significant plastic deformation before failure. This is common in ductile metals where the material undergoes necking and void formation prior to final separation. The fracture surfaces are typically rough and fibrous.
- Fatigue Fracture: Occurs due to repeated cyclic loading, leading to crack initiation and propagation until final failure. This is a significant concern in engineering applications where components experience fluctuating stresses.
- Creep Fracture: Results from prolonged exposure to high temperatures and sustained stresses, leading to gradual deformation and eventual failure. This is a concern in high-temperature applications like power generation and aerospace.
- Impact Fracture: Caused by sudden, high-velocity impact forces. This type of breakage often involves a combination of brittle and ductile fracture mechanisms.
3. Factors Influencing Breakage:
Numerous factors contribute to the likelihood and severity of breakage:
- Material Properties: Strength, toughness, ductility, brittleness, and microstructure play critical roles.
- Loading Conditions: The magnitude, rate, and type of applied load significantly influence the failure mechanism.
- Environmental Factors: Temperature, humidity, and corrosive environments can weaken materials and increase susceptibility to breakage.
- Geometric Factors: Stress concentrations at corners, holes, or other geometric discontinuities can initiate cracks.
- Pre-existing Defects: Flaws, inclusions, or micro-cracks within the material can act as stress concentrators and trigger premature failure.
4. Characterization and Prediction:
Various methods are employed to characterize and predict breakage:
- Mechanical Testing: Tensile, compression, shear, and fatigue tests are used to determine material strength and failure properties.
- Fracture Mechanics: This field utilizes mathematical models to predict crack initiation and propagation.
- Non-destructive Testing (NDT): Techniques like ultrasonic inspection, radiography, and magnetic particle inspection are used to detect flaws and assess material integrity.
- Finite Element Analysis (FEA): Computer simulations are employed to model stress distributions and predict failure locations.
5. Mitigation and Prevention:
Several strategies can be implemented to mitigate or prevent breakage:
- Material Selection: Choosing materials with appropriate strength, toughness, and resistance to the expected loading conditions.
- Design Optimization: Minimizing stress concentrations through appropriate design features and geometry.
- Heat Treatment: Improving material properties through heat treatment processes.
- Surface Treatments: Enhancing surface hardness and resistance to wear and corrosion.
- Regular Inspection and Maintenance: Identifying and addressing potential problems before they lead to catastrophic failure.
6. Real-World Applications:
The importance of understanding breakage is evident across various applications:
- Manufacturing: Optimizing manufacturing processes to minimize material waste and product defects.
- Construction: Ensuring structural integrity and safety of buildings and infrastructure.
- Aerospace: Designing aircraft and spacecraft components to withstand extreme loads and environmental conditions.
- Automotive: Improving the durability and safety of vehicle components.
- Medical Devices: Ensuring the reliability and safety of implantable medical devices.
Closing Insights: Summarizing the Core Discussion
Breakage is a multifaceted phenomenon with far-reaching consequences across numerous fields. By understanding the various types of breakage, the factors that influence it, and the methods used to characterize and predict it, engineers and scientists can develop strategies to mitigate risk, enhance product performance, and optimize processes. The continued research and development in this field are crucial for pushing the boundaries of material science and engineering, leading to more resilient and reliable products and systems.
Exploring the Connection Between Material Microstructure and Breakage
The relationship between material microstructure and breakage is pivotal. Microstructure, referring to the arrangement of grains, phases, and defects within a material, profoundly influences its mechanical properties and susceptibility to breakage. Understanding this connection is crucial for designing materials with enhanced durability and resistance to failure.
Key Factors to Consider:
- Grain Size and Orientation: Finer grain sizes generally lead to improved strength and toughness, while preferred grain orientations can impact fracture behavior.
- Phase Distribution: The distribution and characteristics of different phases within a material can affect its overall strength and fracture resistance.
- Presence of Defects: Voids, inclusions, and dislocations can act as stress concentrators and initiate cracks, leading to premature failure.
- Grain Boundaries: Grain boundaries can act as barriers to crack propagation, enhancing material toughness.
Roles and Real-World Examples:
In steel, for example, a finer grain size achieved through controlled cooling (quenching) results in increased strength and hardness, improving resistance to brittle fracture. In contrast, coarse grain structures are more susceptible to crack propagation and can lead to lower toughness. The presence of brittle inclusions, such as carbides in steel, can significantly reduce overall material toughness and increase the likelihood of brittle fracture. In composite materials, the interfacial bonding between different constituents plays a crucial role in determining their overall strength and fracture resistance.
Risks and Mitigations:
The presence of defects in the microstructure presents a significant risk of premature breakage. Techniques such as heat treatment, thermomechanical processing, and careful control of material processing parameters can be used to refine the microstructure, minimizing defects and improving fracture resistance. Advanced characterization techniques, such as electron microscopy, are used to analyze the microstructure and identify potential weaknesses before failure occurs.
Impact and Implications:
Understanding the influence of microstructure on breakage allows for the development of materials with tailored properties for specific applications. This understanding is critical in designing materials for demanding environments, where durability and reliability are paramount.
Conclusion: Reinforcing the Connection
The interplay between material microstructure and breakage is complex but crucial for optimizing material performance. By carefully controlling the microstructure and minimizing defects, engineers can design materials with enhanced strength, toughness, and resistance to failure, significantly impacting various industries.
Further Analysis: Examining Material Defects in Greater Detail
A closer look at material defects reveals their crucial role in shaping breakage behavior. Defects, ranging from microscopic dislocations to macroscopic cracks, disrupt the regular atomic arrangement within a material, creating regions of stress concentration that can initiate and propagate cracks. These defects can be intrinsic (inherent to the material's formation) or extrinsic (introduced during processing or service).
Types of Material Defects:
- Point Defects: These are imperfections at the atomic level, such as vacancies (missing atoms) and interstitial atoms (atoms occupying spaces between lattice sites).
- Line Defects (Dislocations): These are linear imperfections in the crystal lattice, influencing plastic deformation and crack initiation.
- Planar Defects (Grain Boundaries, Stacking Faults): These are two-dimensional imperfections separating different crystallographic orientations or stacking sequences.
- Volume Defects (Voids, Inclusions): These are three-dimensional defects that can significantly weaken the material and act as stress concentrators.
- Macroscopic Cracks: These are large-scale cracks that can propagate under stress, leading to catastrophic failure.
Influence of Defects on Breakage:
Material defects significantly influence breakage behavior by:
- Acting as Stress Concentrators: Defects create regions of high stress concentration, reducing the overall strength of the material.
- Initiating Crack Formation: Defects can serve as nucleation sites for crack formation, leading to premature failure.
- Facilitating Crack Propagation: Defects can act as pathways for crack propagation, reducing material toughness.
Mitigation Strategies:
Strategies to mitigate the negative effects of material defects include:
- Careful Material Processing: Controlling processing parameters to minimize defect formation.
- Heat Treatment: Modifying the microstructure to reduce defect density or enhance crack resistance.
- Alloying: Adding alloying elements to improve material properties and reduce susceptibility to defects.
- Surface Treatments: Enhancing surface integrity to prevent crack initiation.
FAQ Section: Answering Common Questions About Breakage
Q: What is the difference between brittle and ductile fracture?
A: Brittle fracture occurs suddenly with little to no plastic deformation, while ductile fracture involves significant plastic deformation before failure.
Q: How can fatigue fracture be prevented?
A: Fatigue fracture can be prevented through careful design to avoid cyclic loading, material selection with high fatigue strength, and regular inspection and maintenance.
Q: What role does microstructure play in breakage?
A: Microstructure significantly influences material properties and susceptibility to breakage. A refined microstructure with minimal defects generally leads to improved strength and toughness.
Q: How can non-destructive testing help prevent breakage?
A: Non-destructive testing allows for the detection of flaws and defects within materials without causing damage, enabling preventative maintenance and early detection of potential failure points.
Practical Tips: Maximizing the Benefits of Breakage Understanding
-
Understand Material Properties: Thoroughly understand the mechanical properties of the materials used in your application.
-
Analyze Loading Conditions: Carefully analyze the types and magnitudes of loads your components will experience.
-
Minimize Stress Concentrations: Design components to minimize stress concentrations through appropriate geometries and features.
-
Implement Non-Destructive Testing: Regularly inspect components using NDT techniques to detect flaws and assess material integrity.
-
Develop Preventative Maintenance Programs: Implement proactive maintenance schedules to identify and address potential problems before they lead to failure.
Final Conclusion: Wrapping Up with Lasting Insights
Breakage, while seemingly a simple concept, encompasses a wide range of complex phenomena with significant implications across numerous disciplines. By understanding the various types of breakage, the underlying mechanisms, and the factors influencing it, we can develop innovative strategies to improve material performance, enhance product durability, and ensure safety and reliability in various applications. Continued research and development in this field remain crucial for addressing the evolving challenges associated with breakage and unlocking new possibilities for material science and engineering.
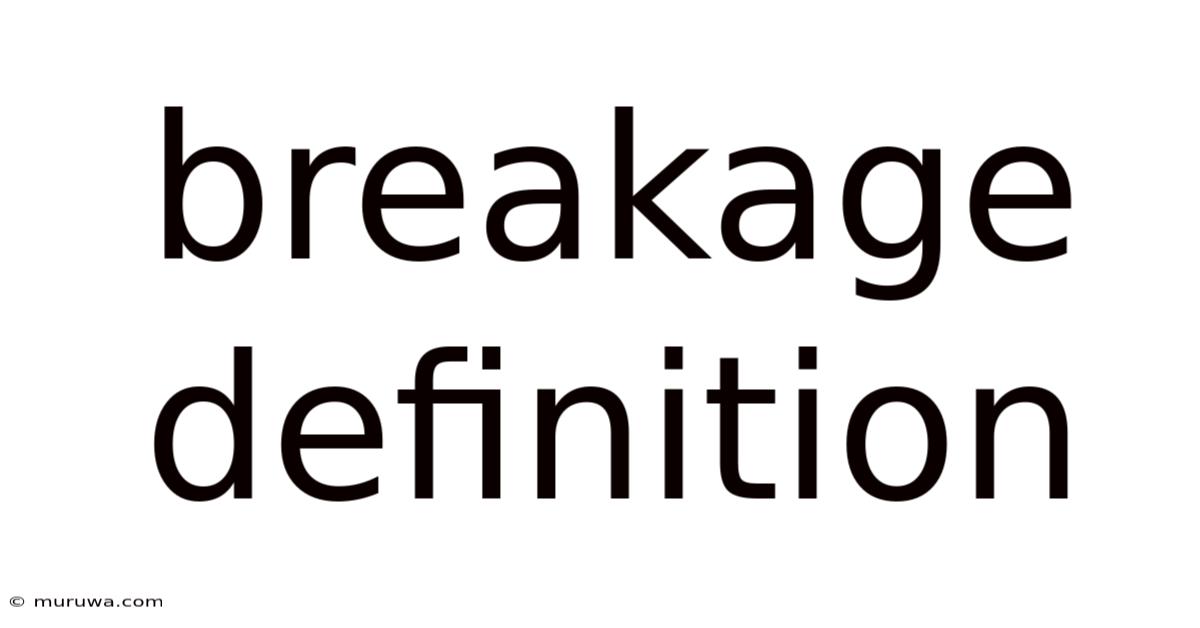
Thank you for visiting our website wich cover about Breakage Definition. We hope the information provided has been useful to you. Feel free to contact us if you have any questions or need further assistance. See you next time and dont miss to bookmark.
Also read the following articles
Article Title | Date |
---|---|
Bond Buyer 20 Definition | Apr 22, 2025 |
Bona Fide Foreign Resident Definition | Apr 22, 2025 |
Why Is 0 Inflation Bad | Apr 22, 2025 |
Boiler Room Definition How It Operates Common Scams | Apr 22, 2025 |
How Does Investing Help You Beat Inflation | Apr 22, 2025 |